冲压成形工艺开发及量产成形改善新模式
2016-09-18 by:CAE仿真在线 来源:互联网
随着工业的不断发展,模具行业数字化调试,已经成为不可逆转的主流趋势。前期成形工艺进行数字化模拟仿真运算,模具制作完成后量化成形性和与仿真运算的验证一直是存在盲点。当成形能力极限检测分析(FLD)技术从钢材力学实验逐步运用于冲压成形稳定的时候起,有效的弥补了模具成形调试的量化缺陷。从方形的检测网格到圆形的检测网格,到后来圆点拍照扫描检测。FLD的检测手段和技术也在不断的发展和进步,其涵盖的数据量也越来越丰富,逐步实现了与前期仿真的模拟的数据平台的构建。因此,本文主要讲述目前FLD技术与CAE数据平台构建、对比、调试运用和改善。
FLD、CAE各自优势特点
FLD是通过材料杯裂实验得到工程应力失效曲线作为材料成形能力极限依据。根据印制网格变化有效的观察材料流动和应力变化。成形能力极限分析运用特点:⑴网格件压制,可以清晰观察晶格变化,判断材料流动趋势;⑵检测材料厚度变化,根据临界厚度和危险厚度,抓住调试重点;⑶晶格应变检测数据反馈在成形极限曲线(FLC)中,直观反应与失效曲线、临界曲线距离,实现成形性数字量化。
AutoFormCAE模拟计算对于模具调试的运用特点:⑴工艺不变情况下进行虚拟调试;调整定位、更改材料尺寸、更改拉延筋强度等;⑵进行数模工艺更改后,验证整改理论效果;⑶模拟结果中,可观察到产品各处晶格应变和材料厚度的理论变化。
在模拟文件中通过成形能力极限图的运用,可以提交预示出成形风险,如图1所示。由此可见,FLD是从实际情况作出成形量化分析。CAE是从理论情况进行的数字模拟分析。两者结合相互支持,得到理论和实践构建量化平台通过数字平台的对比,可以快速找到调试方向,确定调试最佳更改量,有效量化更改效果。
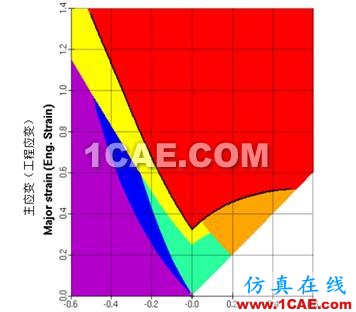
图1 成形能力极限图
实施案例一
江铃某车型侧围内板在工艺开发初期,CAE模拟分析产品轮毂圆角处存在过渡减薄(材料减薄低于20%),有成形性风险,需要产品设计变更。产品工程师则认为后期模具调试可以实现。模具实际调试过程中,产品轮毂圆角出现了成形不稳定缩颈、破裂的情况,产品成形性需要提升。产品检测的FLD图,如图2所示,型面上已经有成形危险点处于临界区域。该点的应变状态为拉伸应变。
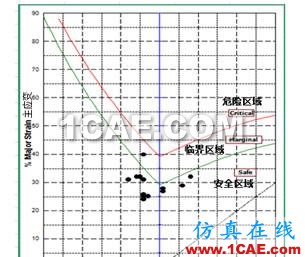
图2 产品检测的FLD图
对材料使用润滑油压制拉延件进行FLD检测。目前FLD检测系统有两种:通过Argus网格应变检测系统进行网格拍照检测;通过测量尺,做网格应变检测。两种方式各有特点:⑴人工检测便于现场测量,直接指导现场调试,可以应对各种复杂区域检测,产品网格存在轻微拉伤不影响产品检测。缺点在于测量点数受到限制,只可关键部位测量,不是有经验员工会存在检测误差;⑵Argus检测系统,拍照自动识别检测速度快,检测精度稳定。缺点在于对网格的印制质量要求比较高,产品造形复杂区域拍照识别会受到影响。对与产品轻微拉伤和侧壁,拍照网格识别存在困难,需要光照较好的条件下拍照,检测结果要处理周期才能得出。基于以上原因本次产品的重点区域在R角尖点,人工检测不存在检测盲点,造形复杂的区域可以做多次细致测量。根据钢厂提供的材料力学参数、FLC失效曲线,通过经验公式计算可得到材料详细的FLD图,再通过拉延件网格测量按工程应力公式进行计算,得到产品检测部位的网格应变极限情况。检测数据危险点距离FLC曲线只有4%裕度。成形稳定性存较大风险。
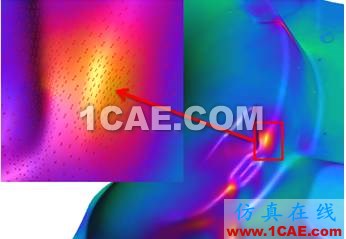
图3 CAE的模拟分析结果
CAE分析结果如图3所示,在轮毂处晶格应变均为平面应变,材料变化剧烈,易失效。成形性提升,须完成主应变减小,副应变为负(改变平面应变的情况)的应变调整。
相关标签搜索:冲压成形工艺开发及量产成形改善新模式 Autoform分析培训班 Autoform汽车模具仿真 Autoform视频教程 Autoform资料下载 在线软件培训 汽车钣金代做 Fluent、CFX流体分析 HFSS电磁分析 Ansys培训 Abaqus培训 有限元培训 Solidworks培训