基于AutoForm分析零件成形时冲击线的控制方法【转发】
2019-04-25 by:CAE仿真在线 来源:互联网
对于汽车外覆盖件,其外观质量尤为重要。外观零件的质量缺陷如冲击线、滑移线等,在涂装工艺后,肉眼观察清晰可见,严重影响零件的外观质量。对于车身A面零件,通常会在冲压工艺方案制订前期重点考察,通过多项CAE评判指标对冲击线进行评价,使其减轻或留在非外观面区域。否则,后期对拉深模进行大范围整改会造成大量人力、物力的浪费。
现针对某车身B面零件的表面质量缺陷进行整改,因前期未对侧围外板与举升门搭接区域的B面流水槽处零件进行成形分析,工艺方案设计阶段也未进行冲击线考量,导致成形零件不能满足要求。以下在保留原拉深模的基础上对其结构进行局部改进使其达到质量要求,整改过程具有很大的局限性和挑战性。
//冲击线//1
冲击线产生原因冲击线是在拉深成形过程中,板料与凹模或拉深筋接触时,由于凹模圆角局部应力集中,在材料表面产生局部硬化从而形成冲击痕迹。在零件的后续成形过程中,这些冲压的带状痕迹会随着材料的流动而移动,最终在板件上形成带状撕裂。
2
冲击线的类型冲击线产生的形式及分类较多,总体上可分为一次冲击线和二次冲击线。一次冲击线是凹模入模圆角在板料上产生的冲击线,如图1所示。
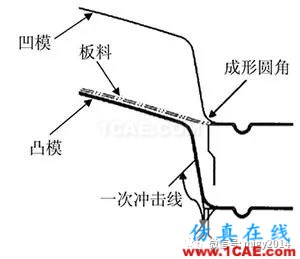
图1 一次冲击线产生
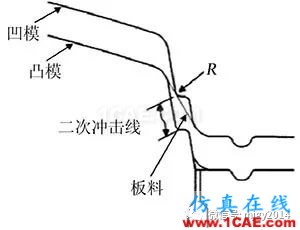
图2 二次冲击线产生
二次冲击线是由非凹模入模圆角上的凸模产生的冲击线,一般是由于零件自身的特征R角产生,如图2所示。
3
冲击线质量问题的解决思路通常情况下,冲击线的产生是不可避免的,通过实际经验,冲击线的解决思路主要有2个方面:①通过减小凹模圆角的表面接触应力,从根本上避免冲击线的产生;②通过降低压料面的形状或增加1个二级台阶,以减少冲击线过多的流入外观面。
//AutoForm软件的冲击线判断方法//1
投影测量法首先,在AutoFormR7版本的Evaluation选项卡中,选取SkidLines评价,再通过AddToolLine选取凹模工具体上成形圆角的点,软件会自动生成模具的标记线,最后点击Apply生成冲击线产生的区域。
通过此方法可明确标记出凹模圆角或凹模圆角在板料上流过的区域,基本可以确定冲击线产生的范围。但并不是凹模成形圆角所流过的区域都会产生冲击线,需要考虑材料表面的最大接触应力,并结合其他参数进行判断。
2
最大接触应力及反弯曲应变最大接触应力反映了在整个成形过程中,凹模圆角或凸模圆角加载在板料上的最大法向接触应力,如图3所示。接触应力过大会导致板件开裂,也可能导致划伤,即冲击线,影响零件的表面质量。

图3 最大接触应力示意图
最大接触应力的默认值为40MPa,通过默认值可以查看冲击线产生的区域范围,在此变量的显示下,凸模圆角产生的最大接触应力也会显示在板件上,但因其未滑过圆角且在反面,不会产生冲击线。
反弯曲应变是成形过程中曲率的减小,其值是成形过程中最大曲率减去当前曲率,再乘以料厚的一半,即反弯曲应变=(最大曲率-当前曲率)×料厚/2,只要曲率一直保持增长,其反弯曲应变为0,一旦曲率减小,反弯曲应变将会显示出相应的差值。
反弯曲应变为无单位参数,通过软件在结果设置中勾选,在CAE结果中查看,其默认上限值为0.05,超过0.05可以看到冲击线流过的区域。
//应用实例//1
冲击线问题工艺方案设计前期未对工艺方案中的冲击线进行管控及评估,如图4所示,零件深色区域为整车外观的B面,即举升门开启后的外观可见面。流水槽零件如图5所示,材质为CR340,料厚0.75mm。
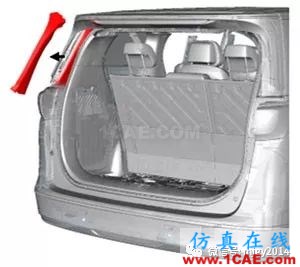
图4 流水槽所处的外观区域
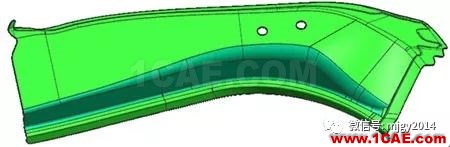
图5 流水槽零件
零件的整体成形工艺方案为:①拉深、切边;②冲孔;③翻边;④翻边侧切边、侧冲孔;⑤侧翻边、冲孔。其中外观面底部圆角R3.75mm为一次成形,工序①未放大R角,但此R角在后工序仍有压料器进行整形。
冲击线产生的根本原因是:凹模圆角与板料的表面接触应力过大,在材料表面产生的亮痕随着拉深深度的增加,冲击线流入外观面。
2
零件的冲击线与CAE的对比分析图6所示为产生冲击线的零件,肉眼在自然光下观察可见局部区域存在冲击线缺陷,无法满足外观质量需求。
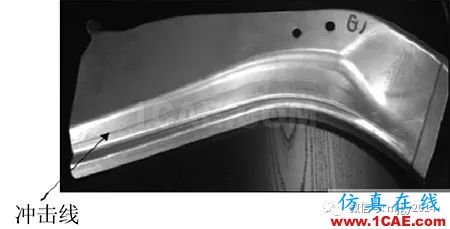
图6 现场零件冲击线
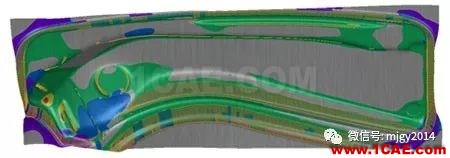
图7 投影测量法显示的冲击线
图7所示为流水槽出现质量问题CAE源文件,采用投影凹模测量法,可明显看出冲击线流入外观面的区域。
通过调整反弯曲应变参数,由于成形过程中零件成形表面曲率的减小,可明显看到冲击线产生的区域,如图8所示。
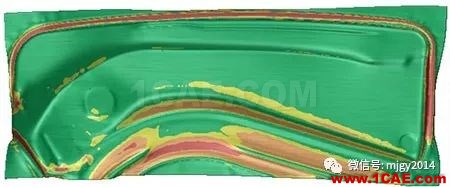
图8 反弯曲应变变量下显示的冲击线
通过调整最大接触应力变量,可明显看到冲击线产生的区域与上述一致。由此可知,利用AutoForm软件在工艺方案设计前期进行分析可准确预测冲击线产生的结果,可为后期模具零件型面的整改提供可靠依据。
3
冲击线问题的整改思路根据上述分析,避免冲击线产生的解决方案:①减缓或不让其产生;②让冲击线避免流入外观面。
01采用第1种方案并用CAE软件进行整改方案的辅助设计验证。
第一步:将产生冲击线的R角在工序①成形圆角放大,由R3.75mm改为R5mm,放大圆角局部的最大接触应力面积大幅缩小,反弯曲应变也减小。由此可知,放大成形圆角对减小冲击线具有明显的改善作用。
第二步:采用投影凹模测量法,检验成形圆角流过的范围。由图9对比可知材料流过成形圆角的范围一致。
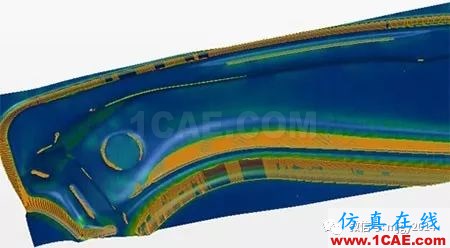
(a)R角放大后
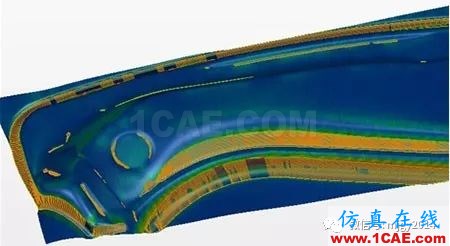
(b)R角放大前
图9 成形圆角流过的范围
综合CAE仿真结果的对比可知,放大局部成形圆角能有效减少冲击线的产生,同时流过成形圆角的材料范围没有变化。
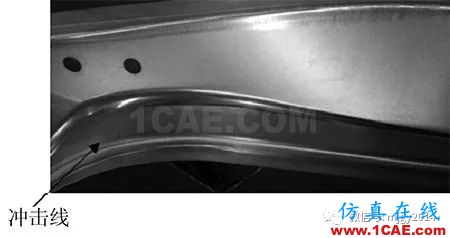
图10 放大成形圆角后的零件
凹模成形圆角通过机械加工放大成形圆角至R5mm后进行现场试模,如图10所示,能减少部分冲击线流入零件B面,但仍在尾部有部分冲击线存在,需持续优化。
02采用第2种方案,采取减小冲击线一侧的材料流入即减少流过成形R角的材料,同样采用CAE软件进行先期整改方案的辅助设计,在AutoForm软件中创建并增加一条实体筋同时放大成形圆角至R6mm。根据CAE结果可知产生的最大接触应力基本控制在圆角范围内,且反弯曲应变值也在可接受范围内。
最终具体方案实施
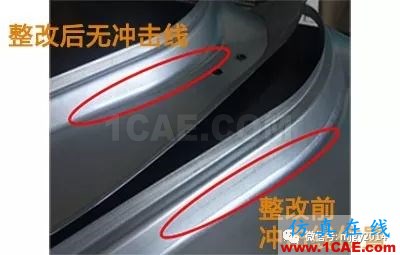
图11 整改前后的零件对比
凹模成形圆角放大至R5mm,同时压边圈通过机械加工、烧焊、增加一条拉深筋后,保证了冲击线留在非外观面的区域,整改前后的零件对比如图11所示。
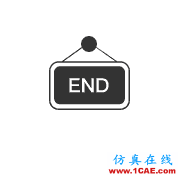
▍内容来源:《模具工业》2018年第12期
▍原文作者:祝林,郑德兵
▍作者单位:泛亚汽车技术中心有限公司
相关标签搜索:基于AutoForm分析零件成形时冲击线的控制方法【转发】 Autoform分析培训班 Autoform汽车模具仿真 Autoform视频教程 Autoform资料下载 在线软件培训 汽车钣金代做 Fluent、CFX流体分析 HFSS电磁分析 Ansys培训 Abaqus培训 有限元培训 Solidworks培训