高强钢的成形方法及应用
2016-09-26 by:CAE仿真在线 来源:互联网
(作者:尤 超 文章来源:瑞典SSAB钢板有限公司)
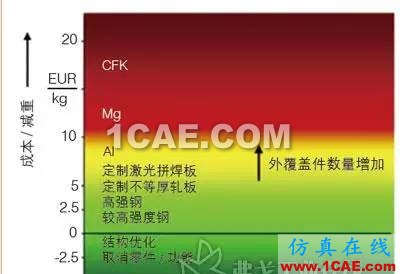
与铝合金及镁合金相比,先进高强钢因其成本低而具有很强的市场竞争力,在汽车轻量化、提高安全性及节能减排等方面,都展现出了广阔的应用前景。然而,在先进高强钢的应用过程中,减薄和高强两大优势却对成形工艺提出了新的挑战。本文简述了先进高强钢的三种常用成形方法。
节能、安全和环保是当今世界汽车发展的主题。据分析,减少汽车自重是降低汽车燃油消耗及减少排放的有效措施之一。由于钢铁材料在强度、塑性、抗冲击能力、回收使用及低成本方面具有综合的优越性,其在汽车材料中的主导地位仍是不可动摇的。随着先进高强钢 (AHSS) 在汽车制造中的比例不断增大,广泛应用于汽车车身、底盘、悬架和转向等零部件上,用高强度钢板代替普通的低碳冷轧钢板、铝合金和镁合金等已成为未来的主要发展方向之一。
图1所示为德国宝马汽车公司的研究成果:以先进高强钢为基准,每减重1kg时各种材料、工艺等所带来的成本变化。其中,用铝每减重1kg,成本增加7.5欧元左右;用镁每减重1kg,成本增加12.5欧元左右。
先进高强钢的定义
先进高强钢具有优良的材料性能,由于迎合了超轻钢车身先进车辆概念(ULSAB-AVC)的安全、节能和经济的先进理念,先进高强钢在汽车工业轻量化中得到了日益广泛的应用。目前,市场上的先进高强钢主要有双相钢(DP)、复相钢(CP)、相变诱发塑性钢(TRIP)和马氏体钢(MART)等(见图2),强度范围为500~1600MPa。其中,双相钢和马氏体钢是目前市场上应用最广泛的先进高强钢,瑞典SSAB公司生产DOCOL1500M是目前市场强度最高的冷轧马氏体钢。
先进高强钢的成形方法
目前常用的先进高强钢的成形方法主要有:辊压成形、冷冲压成形和热冲压成形。
1.辊压成形工艺
辊压成形(又称滚压成形)工艺是通过顺序配置的多道次成形轧辊,把卷材、带材等金属板带不断地进行横向弯曲,以制成特定断面的型材。
辊压成形工艺具有以下优点:
(1)最高可生产强度为1500MPa的零件,如某前碰撞横梁(见图3)采用DOCOL1500M(抗拉强度1500MPa)替代DOCOL1200M(抗拉强度1200MPa),辊压成形后板厚减少0.2mm,质量降低0.75kg。
(2)生产效率高,适合于大批量生产,与冲压工艺相比效率提高10倍以上,制造成本大幅降低;
(3)加工产品的长度基本不受限制,可实现不同车型同一零件的模块化设计,降低制造成本,如某品牌3款不同车型车门槛板(见图4)设计为同一截面,材料牌号:DOCOL1000DP,抗拉强度:1000MPa,3款车型共用同一生产线,实现了生产线共用;
(4)能有效解决超高强度钢的回弹现象,可达到极小成形半径;
(5)不需专用成形模具;
(6)产品的表面质量好,尺寸精度高;
(7)在辊压成形生产线上可以集成其他的加工工艺,如冲孔、焊接及压花等。如某辊压成形的车门槛板(见图5),材料牌号:DOCOL1400M,抗拉强度:1400MPa,冲孔在辊压过程中完成;
(8)材料利用率高,一般可达到90%以上;
(9)生产噪声低,无环境污染。
辊压成形工艺加工出来的型材其断面结构合理、几何尺寸精确,体现了现代社会对材料轻量化、合理化及功能化的使用要求。辊压成形采用先进的高效生产工艺,使成形截面达到最好的力学性能,特别适用于超高强度钢零件的加工成形,其有效地解决了超高强度钢的回弹,并极大地降低了制造成本,推进了超高强度钢在汽车工业中的应用。采用该工艺加工的典型零件有汽车前后碰撞横梁、车门槛板和座椅滑轨等。
辊压成形工艺的不足之处在于要求所加工零件截面为等截面,对零件设计提出了更高的要求。
2.冷冲压成形
冷冲压成形是用压力机通过模具将料板冷冲压成形产品,主要步骤有拉延成形、切边和整形等。
冷冲压成形工艺具有以下优点:
(1) 最高可生产强度为1400MPa的零件;
(2) 生产线成本不高,普通零件如车门防撞梁用800t的液压机或机械压力机即能满足生产要求;
(3) 零件生产效率比较高;
(4)可以使用AUTOFORM、DYNAFORM等软件进行成形模拟分析。
其不足之处在于:
(1)材料利用率不高,根据零件形状、模具设计等不同,一般为40%~75%;
(2)产品回弹、褶皱和壁翘曲难以控制,模具调试时间长;
(3)模具设计和加工复杂;
(4)生产过程中噪声大,特别是切边工序;
(5)太过于复杂的零件成形困难,需要多步成形,成本增加,如汽车B柱。
高强度钢的冷冲压件在生产时,遇到的最大难题是成形件尺寸精度难以保证。为了解决这一难题,需要用AUTOFORM等软件进行成形模拟分析,并多次调模以减少回弹及壁翘曲。但对于一些非等截面零件,因为不能采用辊压成形,而冷冲压成形相对于热冲压成形生产成本低,所以也广泛应用于汽车零部件的制造中。其中最典型的零件如:车门防撞杆、底板纵横梁和车顶纵横梁等。如图6所示,冷冲压成形的车门防撞梁,材料牌号:DOCOL1200M,替代热成形零件。
3.热冲压成形
热冲压成形工艺过程首先把常温下强度为500~600MPa的高强度硼合金钢板(俗称硼钢,如20MnB5、22MnB5和30 MnB5等) 加热到900~950℃并保持5~10min,使之均匀奥氏体化,然后送入内部带有冷却系统的模具内热冲压成形,之后保压快速冷却淬火(冷却速度> 50℃/s),使奥氏体转变成马氏体。成形件因而得到强化硬化,屈服强度可以达到1000MPa以上,抗拉强度可以达到1500MPa以上。
高强度钢板的热冲压成形工艺的基本流程是:落料—预成形—加热—冲压成形—去氧化皮—激光切边冲孔—防锈处理,并在冲压成形和保压定形阶段同时进行板件淬火。图7所示为热冲压成形的工艺流程。
这项工艺的核心内容在于其冲压成形中的保压定型过程以及模具的冷却。其优点是:
(1)最高可生产强度为1500MPa的零件;
(2)高温下材料塑性好,成形能力强,可成形比较复杂的零件,如汽车B柱;
(3)高温下成形没有回弹,成形极限高,实现高精度成形,成形后零件强度等性能指标大幅度提高。
不足之处在于:
(1)生产线复杂,设备投资大;
(2)生产、维护和保养复杂,生产成本高;
(3)模具设计和加工复杂;
(4)生产节拍慢;
(5)零件强度容易受到生产零件的影响而产生波动,生产过程控制要求极为严格。
热冲压成形技术因为其较强的成形能力仍然在汽车工业中有着广泛的应用,其中最典型的零件如汽车B柱(见图8),材料牌号:20MnB5;板厚:1.85mm;成形后抗拉强度:1500MPa。
高强钢板成形技术发展趋势
尽管高强钢板成形技术的研究已取得了长足的进步,但由于高强钢板成形性能的特殊性及复杂性,还需要不断地进行技术创新。在此,简单介绍一些高强钢成形方面的最新研究。
1.不等厚板热成形技术
该技术可以实现不同部位不同强度、不同厚度及不同材质,主要优点有:大大减轻车身重量;减少汽车零部件的数量,因而减少了模具数量;提高了材料利用率,废料大大减少;结构功能与工艺性能得到提高。
2. 柔性辊压成形技术
与传统等截面辊压成形相比,变截面柔性辊压成形是成形截面沿纵向变化的,因而具有更合理的力学性能,结合材料的使用技术,对超高强度材料零部件进行成形加工,整车质量可进一步降低25%,将成为下一代辊压成形技术的发展方向。国内外,如德国达姆施塔特大学(见图9)、我国北方工业大学(见图10)等在柔性辊压成形方面都颇有研究。
结语
汽车轻量化是大势所趋,而采用先进高强钢是实现轻量化的主要技术途径之一。同时,制造工艺的改进和成形技术的发展,也促进了先进高强钢在汽车制造领域的应用。目前市场上最常用的先进高强钢的成形方法主要有:辊压成形、冷冲压成形和热冲压成形。而就制造成本而言,辊压成形最优,冷冲压成形次之,热冲压成形成本最高。
我国汽车轻量化起步较晚,相关高强钢成形工艺技术与国外有着一定的差距。但我国高校、科研院所、汽车及零部件厂家正积极努力,致力于提高自身的设计能力和制造工艺水平,为加速我国汽车轻量化的步伐,为节能环保做出了一定的贡献。
相关标签搜索:高强钢的成形方法及应用 Autoform分析培训班 Autoform汽车模具仿真 Autoform视频教程 Autoform资料下载 在线软件培训 汽车钣金代做 Fluent、CFX流体分析 HFSS电磁分析 Ansys培训 Abaqus培训 有限元培训 Solidworks培训