硬质PVC管材的生产工艺,一次性讲透彻!
2016-10-18 by:CAE仿真在线 来源:互联网
硬质PVC管材规格和形式很多,其生产工艺流程基本上如图:
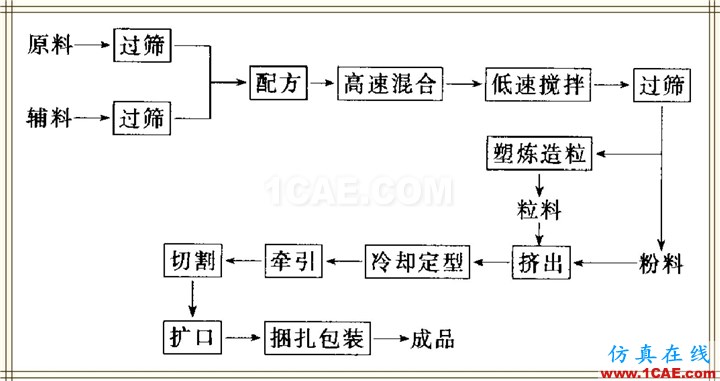
生产工艺流程可分为三个过程:
♥ 1、成型料准备过程(又称挤出前段),包括配方(原料、辅料的前处理、计量、输送)、混合(高速和低速)、过筛(成型粉料)或造粒(粒料)。
♥ 2、挤出成型过程。
♥ 3、定型包装过程(又称挤出后段)。
为了改进管材的加工性能、使用性能和降低成本,需要在PVC原材料的基础上加入稳定剂、润滑剂、填充剂、加工改性剂等助剂。
(一)原料的预处理:原辅料在生产和装运过程中可能混入一些机械杂质,需要对其进行过筛和磁吸处理,除去杂质。
(二)原辅料的计量:按照确定的配方将原辅料精确计量。各组分的称量误差应控制在1%以内。
(三)原辅料的混合:PVC管材的原辅料大多是固体粉料(只有少量助剂是液态),成型料通过物料间对流作用和剪切作用进行混合制备。目前采用高速混合机将原辅料进行混合,再用低速冷混机将混合好的物料进行冷却。
一般高速混合的温度设在100~120℃。为了让助剂充分地与PVC微粒接触,减少填充剂对助剂吸附作用。要求加入PVC树脂后立即启动热混合机,再按:稳定剂→ 各种加工助剂→色料→填充料(碳酸钙),将原辅料全部投入后再启动高速热混合机。混合后需立即冷却,若散热不及时会引起物料分解和助剂挥发。
冷混机的搅拌速度较低,其容积应为热混机的两倍以上。冷混一般温控制在40℃左右时出料,排出的物料还应过筛,除去结块和粘熔料。
原辅料混合工艺流程如下图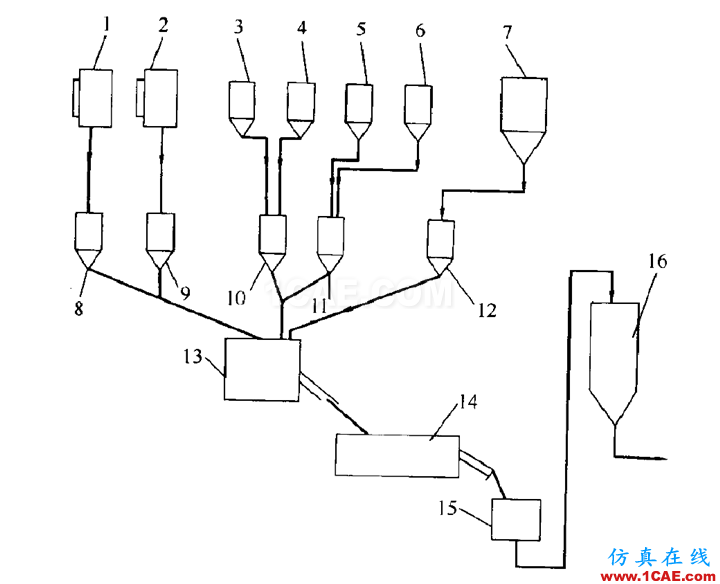
1、2—液体助剂贮槽;3、4、5、6—助剂贮槽;
7—PVC粉贮槽;8、9.—液体助剂计量器;
10、11、12—粉体计量器;13—高速热混器;
14—低速热混器;15—振动筛;16—混合粉贮槽
注:使用单螺杆挤出机生产PVC管材时,干混料不能直接使用,必须经过混炼塑化加工成粒料的工序,粒料的生产方法一般是利用挤出机挤出的混合料细条,经过切割机进行冷切或热切两种方式加工成一定规格的粒料。
二、挤出成型工艺
目前PVC管材的生产大多采用螺杆挤出机进行干法塑化工艺连续操作。
在螺杆挤出机转动时,料斗中的干混料或粒料进入加料筒中,利用摩擦热使混料熔化成熔体,在设备中不断往前流动,各组分受螺杆的搅拌而均匀分散。熔体在机头口模处成型后成连续体被螺杆挤到机外,经冷却凝固,即成管材。
1挤出机的选择管材的挤出机可以用单螺杆挤出机,也可以用双螺杆挤出机。
单螺杆挤出机的最佳挤出量:
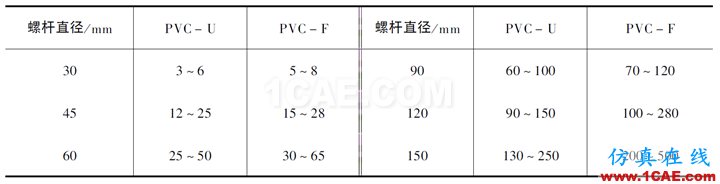
2挤出过程
生产PVC管材的挤出机主要有两种:单螺杆挤出机和导向啮合双螺杆挤出机。
用于生产PVC管材的挤出机螺杆分段见下表:

▷ 1、固体输送区(加料段):料筒温度一般控制在100~140℃。
▷ 2、物料塑化区(熔化段):其温度控制在170~190℃。
▷ 3、熔体输送区(计量段):其温度控制略低一些,一般为160~180℃。
总之,在挤出机实际生产中,根据生产不同规格的PVC管材,选择合适的工艺条件:配方、螺杆转速及各段控制温度等,以达到塑化和挤出量的最佳效果。
3成型过程挤出机连续提供的熔化和具有压力的塑料熔体是通过机头特定的流道进入口模而形成一定的结构和形状。
机头是挤出制品成型的重要部件,它的作用是产生较高的塑料熔体压力并使其成为所需的形状。
聚氯乙烯管材的挤出机头一般都是直线机头(直通式)。对于复合管材和内径尺寸要求严格的管材常采用直角式机头。
直线机头图
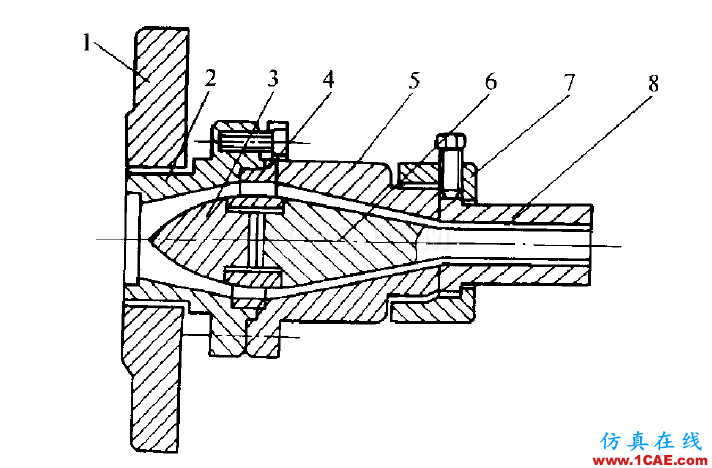
1—卡套;2—连接套模;3—分流器;
4—分流环;5—中套;6—芯棒;
7—锁母;8—口模
三、成型工艺
从机头口模挤出来的管状物要经过冷却,使它变硬而定型。
1定型方式定型方式一般是用定径套进行外径定型和内径定型两种。
(1)外径定型外径定型是使管状物外壁和定径套内壁紧密接触。
要达到这种紧密接触有两种方法,一种是从设在支架中的一个筋和芯棒内的连通孔向管状物内部通的压缩空气,并将挤出的管端封塞,使管内维持比大气压较大而又恒定的压力,为内压定径:
内压定径装置示意图
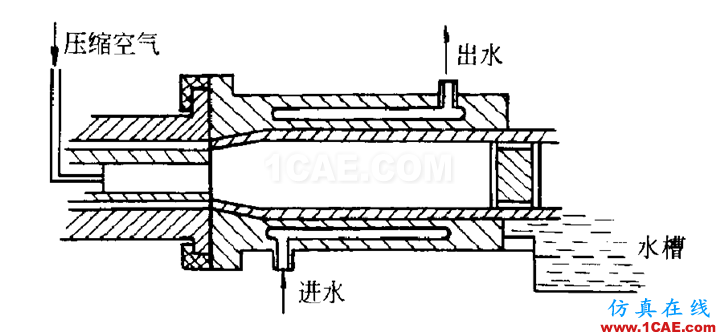
另一种方法是在定径套上沿圆面上钻一排排小孔,用真空抽吸使管状物紧贴套管,为真空定径:
真空定径装置示意图:
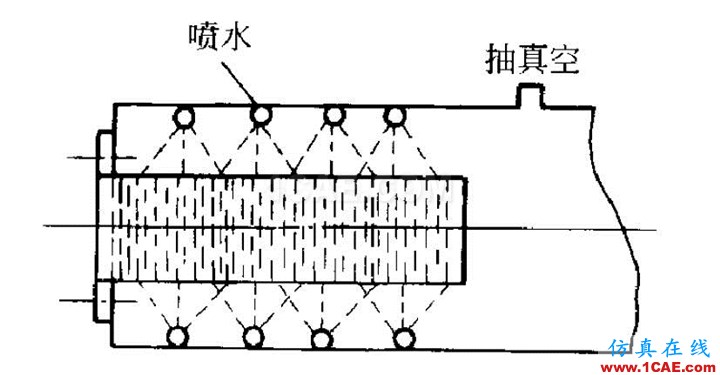
(2)内径定型内径定型常用于直角机头或偏心机头。管材从口模出来后便套在冷却定型芯子上,管材内表面紧贴于定型芯子外壁并迅速冷却硬化而定内径尺寸。为便于冷却水从芯模后部淀入冷却定型芯子,冷却定型芯子连接在芯模延伸轴上,其结构见图:
内径定型法示意图
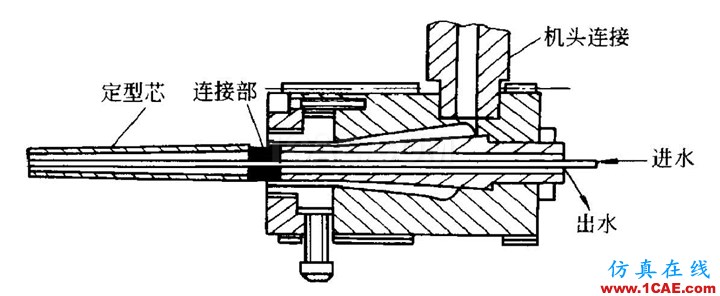
以上二者比较起来,外径定型结构较为简单,操作方便。外径定型的定径套长度一般取其内径的3倍,定径套的内径应略大于管材外径的名义尺寸,一般不大于2mm。
2冷却方法用来冷却管材的方法常用水浸式冷却和喷淋式冷却两种。
(1)水浸式冷却水浸式冷却的装置是冷却水槽,将挤出的管材浸在水槽中进行冷却(见下图):
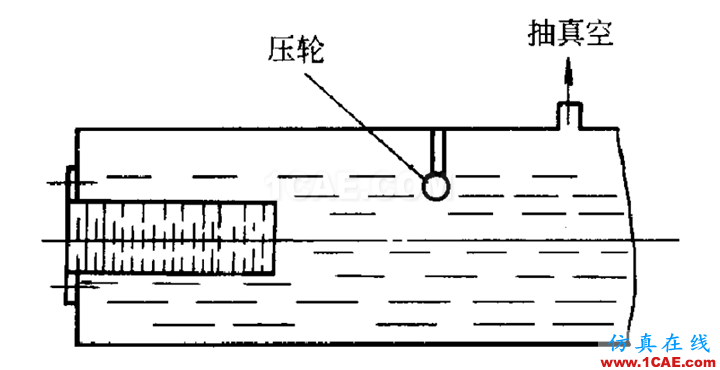
该方法要考虑的是管材在冷水槽中会受到浮力影响,有可能使之发生弯曲变形,尤其是大口径管材,其浮力大,弯曲变形可能性更大。
(2)喷淋式冷却喷淋冷却的装置是喷淋水箱,水箱上装有沿管材圆周均匀分布的喷水头(见下图),控制一定的水量对挤出管材进行喷淋冷却:
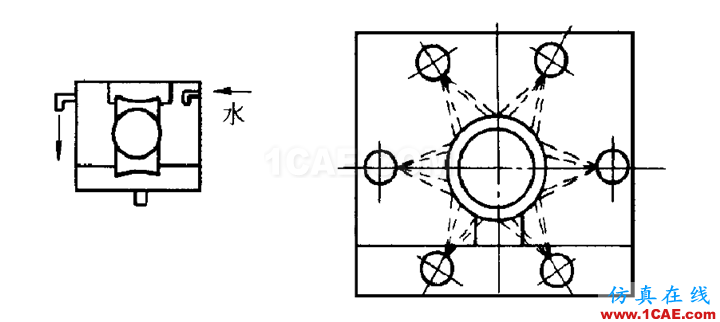
该方法冷却均匀,变形可能性小,小口径管材生产时往往将真空定型与冷却槽设计成一体。总之,要获得光洁度高,尺寸准确,几何形状正确的管材,进行有效的冷却和尽快定型是至关重要的。
四、牵引工艺
牵引装置的作用是给机头挤出的管材提供一定的牵引力和牵引速度,均匀地引出管材,并通过牵引速度调节管子的壁厚。
牵引管材的装置有滚轮式(见下图),和履带式(见下图)两种。
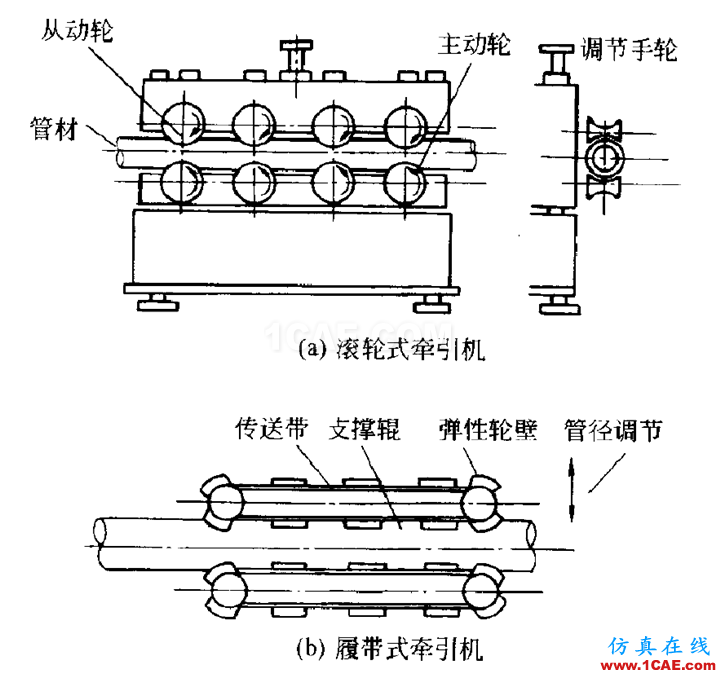
对牵引装置的要求是它们应具有较大的夹持力,并能均匀地分布在管材的圆周上。牵引速度要求十分均匀,并且能无级调速。牵引速度是取决于挤出速度。
五、管材承插口加工工艺
承插口连接是PVC管材的主要连接方式。管材承插口多数是在生产厂家加工形成的。承插口是通过热胀法在扩口机上进行,也有的厂家采用人工扩口。承插口有两种型式,一是平直承插口;二是R型承插口。
△ 平直型承插口采用胶粘剂粘接,主要适用于DN20~200mm的管材。
△ R型承插口采用弹性密封圈连接,主要适用于DN63~630mm的管材。
PVC—U管材的扩口属于塑料二次加工中的热成型工艺。扩口操作大致分几个步骤(R型承插口)。
-
1、将管材一端在加热炉中加热到规定温度,常用的加热方式有油溶加热和电加热。
-
2、将管材加热好的一端趁热插人扩口机头的模芯中,操作扩张顶杆,使其扩成型后再用水喷淋冷却。
-
3、管材冷却后,顶杆回撤,多瓣机头截面缩小,机头就可从扩口面退出。
平直扩口操作时,将管材一端加热好,趁热插入扩口模具中冷却定型即可。
塑料二次加工热成型通常是在高弹态或粘流态进行。
PVC在80℃以下处于玻璃态,在80~160℃范围内,PVC处于高弹态,形态可逆,成型后会产生残存内应力;在温度超过160时,PVC处于粘流状态,表现为可塑性,形态不可逆。
因此,PVC—U管材的扩口温度应在80℃以上。
温度较低时,物料流动性差,扩口后的承插口外观上易产生白化,且由于温度偏低而不能获得大的伸长率而导致扩口破裂,尺寸上表现为稳定性差,轮廓不清楚;
而当成型温度较高时,虽然成型后残存内应力小,但又易造成承插口有折皱、气泡、变色、分解等现象,外观较差,分解严重还会造成强度下降。
PVC—U管材扩口最佳成型温度为160~180℃。
选择管材加热时间的标准是:保持足够的加热时间,使管材达到最佳成型温度,并使温度分布均匀,又不出现变色、分解。
PVC—U热导率低于0.15W/(m·K),导热性差,其适当的加热功率密度是1.5~3.0W/cm²,为使温度分布均匀,加热过程中都采用旋转管材方式。下表所列PVC—U管材的壁厚与加热时间可供参考:加热温度160℃,加热功率密度1.5W/cm²。

注:扩口成型后的冷却亦是很重要的一点。选择冷却条件的标准是:在保证承插口内应力小、耐冲击性好、承插口不变形的前提下,以冷却时间短为原则。自然冷却有利于内应力消除,提高管材耐冲击性,但时间长,生产率低。因此,一般采用水冷,冷却到40~50℃(变形温度以下)。
相关标签搜索:硬质PVC管材的生产工艺,一次性讲透彻! 机械设计培训 机械设计课程 机械设计视频 机械设计技术教程 机械设计资料下载 SolidWorks UG inventor软件应用 Fluent、CFX流体分析 HFSS电磁分析 Ansys培训 Abaqus培训