【技术帖】复合材料汽车前保险杠低速碰撞仿真分析
2016-11-09 by:CAE仿真在线 来源:互联网
汽车发生低速碰撞时前保险杠能够吸收冲击能量,因此研究保险杠的碰撞特性和碰撞过程中的吸能特性是必要的。本文建立汽车前保险杠的三维模型,保险杠横梁采用CFS003/LTM25碳纤维增强环氧树脂复合材料,运用LS—DYNA软件对保险杠在低速碰撞(4km/h)过程中的动力响应特性进行仿真,并对该保险杠系统应力云图,能量变化曲线,横梁变形情况以及加速度时间历程曲线结果进行分析。结果表明:该有限元模型仿真结果正确且复合材料横梁和右吸能盒吸能性能良好而左侧吸能盒吸能效果不佳,为后续保险杠的优化奠定了基础。
关键词:前保险杠;复合材料;LS-DYNA;低速碰撞
正面碰撞问题一直是汽车被动安全性研究的重点和热点[1]。保险杠系统是轿车车身的重要组成部分,其作用为当轿车与其他车辆或障碍物发生碰撞时首先接触的部件,应该能起到保护车身和附件,具体说就是保护翼子板、散热器、发动机罩和灯具等部件的作用。轻微事故时保险杠系统能吸收冲击能量,撞后自动恢复原状,有效地降低了轿车的修理费用。遇上严重的撞车事故时,冲击力经保险横杠被合理导向分散给整个车身,以避免局部区域变形过大,保证乘客有足够的生存空间。由于保险杠在低速碰撞中的重要性,世界各国针对保险杠的耐撞性都制定了具体、详细的法规和试验要求,此外,研究汽车保险杠的碰撞特性和碰撞过程中的吸能特性,对于提高汽车的碰撞安全性具有重要的意义。
J.Hilmann与M.Pass等人采用遗传算法对车辆前保险杠系统进行了耐撞性能研究与改进,并将该方法应用到白车身的设计中[2]。Marcus REdhe使用LS-OPT对汽车吸能盒进行的形状改进,使用神经网络方法来优化吸能盒的几何形状,在减少保险杠横梁的侵入量、刚性墙侵入量和降低纵梁应变的约束条件下来提高车辆的低速碰撞性能,改进后的模型降低了系统的质量,减少了侵入量,改善了低速碰撞性能[3]。章正伟按照欧洲ECE-R42法规要求,建立保险杠有限元仿真模型,并对其进行非线性模拟分析,得出增强保险杆耐撞性的规律[4]。杨永生将整车模型简化为台车模型,根据经验值和仿真结果,设计某一款进口车吸能盒诱导槽的位置和数量,降低了碰撞力的峰值,增加了吸能盒吸收的能量[5]。
本文以汽车前保险杠为研究对象,横梁采用CFS003/LTM25碳纤维增强环氧树脂复合材料,利用LS-DYNA软件对汽车低速碰撞条件下的耐撞性进行仿真分析研究,并在此基础上提出了改进保险杠耐撞性的途径。
1.1 层内损伤模型
层内损伤的分析采用基于传统应力强度理论的预测模型。该模型是以材料内部某点处的应力水平或一定区域的平均应力水平作为失效准则来判定损伤的产生。这就需要建立一套准确合理的损伤失效判定准则,如金属材料常用的Mises强度准则与剪切强度准则,复合材料的失效准则是在均匀各向同性和均匀各向异性材料强度理论的基础上结合复合材料自身的特点,通过大量实验研究和理论研究逐步发展起来的。由于复合材料损伤破坏机理十分复杂,失效准则往往不具有普遍适用性,因此出现了许多失效准则,如Tsai-Hill失效准则、Tsai-wu失效准则、Hashin失效准则、Chang-Chang失效准则等。对于出现损伤的区域其材料力学性能下降,需要使用适当的材料刚度 退化方式,对损伤区域的材料性能进行调整。
1.2 分层损伤模型
大量研究结果表明,复合材料层合板的分层损伤仅在纤维铺设角度不同的两相邻子层之间的界面处产生、扩展。因此,在可能发生分层的子层间引入一层厚度极薄界面单元,通过界面单元的失效破坏,可以真实有效地模拟预测分层损伤的产生,及其扩展过程。如1图所示为一典型三维界面单元,它由连接对应的上下子层的两个表面构成[7]。由于界面层非常薄,初始界面单元的上表面和下表面对应节点间的距离非常小。其中局部坐标系e1为界面单元的厚度方向,该方向的界面力P1与开裂模式I相关联;e2,e3为界面单元的两个面内相互垂直方向,其界面力p2,p3分别与开裂模式II,III相关联。三种裂纹尖端的开裂模式如图2所示,分别为:张开型、滑开型和撕开型。
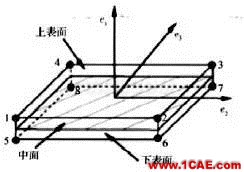

与界面上下表面间相对位移


(i=1,2,3) (1)
式(1)中,

为三个方向的界面力,

为相应的界面相对位移。
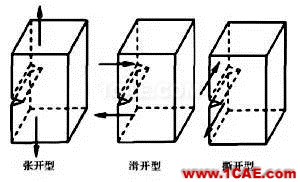
图2 三种开裂模式示意图
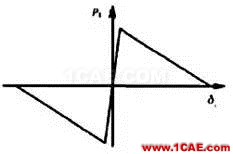
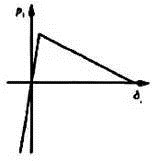
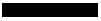
(2)式(2)中,

(i=1,2,3)为界面强度,判定准则


(3)式(3)中,

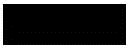
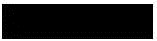
(5)或

(6)式中,

2.1 三维模型的建立
常见的保险杠总成主要由横梁,吸能盒,连接板等部分组成。其中横梁和吸能盒都可作为缓冲吸能元件。其吸能效果的好坏将直接影响其安全性能。为对保险杠的低速碰撞响应进行研究,通常独立对以上几个部件建立简化模型进行碰撞仿真研究。建立模型的主要的步骤如下:假定汽车以4km/h的速度碰撞到前方固定的刚性墙。先利用pro/e软件建立三维模型,将其导入HYPERMESH中进行前处理。使用HYPERMESH进行前处理时,采用平均20mm的网格。整个保险杠总成连接关系可直接采用点焊连接,在仿真模型中采用SPOTWELD一维单元模拟。为符合法规要求,需要在简化车体上均匀分布质量单元,在每个节点上赋予300g的质量,则其总体质量等于整车整备质量为1600kg。保险杠总成有限元模型以及碰撞仿真所用到的刚性墙有限元模型如图4所示。其中有限元网格(不含刚性墙)结点数量为13483个,单元数量为13122个。
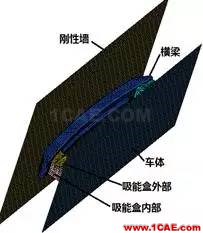
图4 前保险杠有限元模型
2.2 材料的定义
大多数轿车车身所使用的材料为钢材。在车辆前端对车身安全起重要作用的结构,尤其是以保险杠骨架为主的包括与纵梁相联接的汽车吸能盒部分,在低速正面碰撞中,对载荷传递和能量吸收具有重要作用,直接影响到乘员舱的侵入和车辆维修性等方面。汽车吸能结构的设计工作是车辆设计的重要环节,尽管金属材料吸能结构被广泛使用,但树脂基复合材料管件因比刚度高,比吸能大,而且可根据使用要求对其材料组分及结构参数进行逆向设计等优点,故本文横梁材料采用CFS003/LTM25碳纤维增强环氧树脂复合材料,厚度为1.2mm。保险杠系统横梁以及其他组件材料参数分别如表1、表2所示:
表1 CFS003/LTM25碳纤维增强环氧树脂复合材料
名称 | 数值 |
密度ρf/(t/mm3) | 1.45e-9 |
沿纤维方向杨氏模量E1/MPa | 53600 |
垂直纤维方向杨氏模量E2/MPa | 55200 |
剪切模量G12/MPa | 28500 |
泊松比 | 0.042 |
沿纤维方向拉伸强度S1t/MPa | 6180 |
沿纤维方向压缩强度S1c/MPa | 6420 |
垂直纤维方向拉伸强度S2t/MPa | 6520 |
垂直纤维方向压缩强度S2c/MPa | 5560 |
剪切强度S12/MPa | 84 |
名称 |
密度[Rho] t/mm3 |
弹性模量E MPa | 泊松比Nu | 材料号 |
厚度 mm |
刚性墙 | 7.8e-9 | 210000 | 0.3 | MATL20 | 3 |
吸能盒 | 7.89e-9 | 210000 | 0.3 | MATL24 | 1.9 |
车体模型 | 7.8e-9 | 210000 | 0.3 | MATL20 | 3 |
表2 其他关键组件的材料参数
保险杠吸能盒所用材料为LS-DYNA中24号材料,即其关键字为:*MAT_PIECEWISE_ LINEAR_PLASTICITY(分段线性塑性材料模型),保险杠吸能盒为低强度钢,其具有较低的屈服极限,比较容易产生屈服变形,因而能在碰撞过程中迅速进入屈服阶段,依靠屈服变形来吸收碰撞动能。简化的车体模型所用材料与刚性墙一致,都使用LS-DYNA中20号材料,其关键字为:*MAT_RIGID,即为RIGID刚性材料[8]。横梁所用材料选用LS-DYNA材料模型中的54号材料(*MAT_ENHANCED_COMPOSITE_DAMAGE)。该材料本构能很好的模拟正交各向异性复合材料,通过材料主轴设置可方便的定义不同纤维铺设角度,且含有多种失效准则作为各种层内损伤的判定依据[9]。其失效准则及其相应的刚度退化方式是基于Chang-Chang准则扩展补充得到,如表3所示:
表3 Chang-Chang失效准则
失效模式 | 失效准则 | 刚度退化方式 |
基体开裂 |
![]() , ![]() |
![]() |
基体挤压破坏 |
![]() , ![]() |
![]() |
纤维断裂 |
![]() , ![]() |
![]() |
纤维压缩破坏 |
![]() , ![]() |
![]() |

和

分别是纤维方向的拉伸和强度,

和

分别是横向拉伸和压缩强度,

是横向面间的剪切强度。
2.3 接触面的创建
为了防止边对边的渗透及初始渗透,接触厚度尽量采用实际的外壳厚度,有充分的网格密度来正确处理接触的压力分步和防止初始渗透。在保险杠系统与刚性墙之间定义关键字为*CONTACT_SURFACE_TO_SURFACE接触,保险杠系统自身定义关键字为*CONTACT_SINGLE_SURFACE接触。
2.4 边界条件
按照GBl7354.1998的要求,试验车辆低速对中的试验速度为4km/h。在碰撞模拟过程中,为正确地模拟车体与保险杠的约束关系,在低速碰撞过程中,刚性墙六个自由度(三个轴向移动,三个绕轴旋转)全部被约束,即其固定不动。
2.5 连接方式
现代汽车的车身结构通常由构件通过焊接、螺栓联接、铆钉联接等方式连接组成。本模型选用实体的SPOTWELD来模拟焊点连接。
2.6 沙漏的控制
显式算法的一个重要优点便是其计算效率高,而计算的高效率很大一部分来源于单元应力散度计算的单点高斯积分。但单点高斯积分将导致沙漏模态的产生。在进行结构动力学分析时,若不对沙漏模态进行控制,计算将产生数值振荡,如何控制沙漏模态以保证仿真计算的可靠性便成为显式动力分析程序的一个重要课题。控制沙漏模态的主要思想是在单元局部计算时将沙漏粘性应力加到物理应力上。由于车身构件及碰撞变形部件主要是薄壳单元,因此这里仅讨论薄壳单元的沙漏控制算法。使用LS-DYNA中的CONTROL_ENERGY关键字对能量进行控制,其中的HGEN选项,将其值置为1。使用LS-DYNA中的CONTROL_HOURGLASS关键字进行沙漏控制,本文采用LS-DYNA标准的控制选择,该关键字选项卡的IHQ置为1,表示为LS-DYNA默认沙漏能控制。
2.7 时间步长的定义
显式有限元的中心差分法是条件稳定的,只有时间步长小于临界时间步长才能保证计算结果的正确,经过计算,本文的计算时间定为0.08s,计算步长设为10-6s。
3.1 应力云图分析
图5和图6为汽车保险杠系统有限元模型0.03s和0.05s时刻的应力云图。
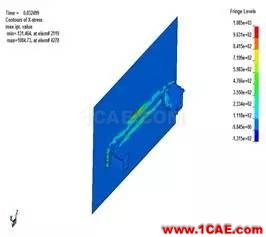
图5 0.03s时刻的应力云图
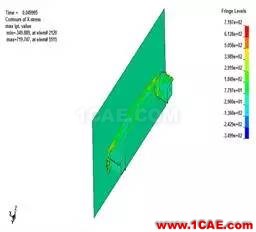
图6 0.05s时刻的应力云图
由图可以看出,保险杠系统最大应力出现在0.03s时刻且位置为横梁最先接触刚性墙部位,由于刚性墙不动,应力会不断从中间部位分布到横梁其他部位,此过程中应力不断衰减,在0.05s时刻最大应力值明显小于0.03s时刻,且发生位置为横梁两侧位置。
3.2 能量曲线分析
碰撞过程中汽车各部件的动力响应是一个涉及几何非线性、材料非线性和复杂的接触摩擦问题的大变形力学过程。在碰撞过程中,碰撞能量的主要传递途径是:(1)通过结构的弹塑性变形吸收一部分能量(内能);(2)通过碰撞车辆之间的速度再分配保留一部分碰撞动能。汽车碰撞过程表征了一个能量守恒、动量交换的瞬态过程,其动能大部分快速转变为变形能(内能),小部分以声能等其它能量耗散掉。能量变化清楚地表现在汽车的碰撞过程中。汽车碰撞开始是撞击体与被撞击体接触、变形由小到大,至最大,而后两体回弹分离,本文中刚性墙不动,汽车将被弹回分离。图7为模型碰撞过程中的能量曲线。
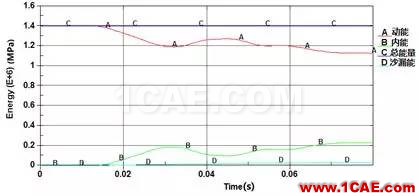
图7 系统能量变化曲线
可以看出,在碰撞过程中,总能量是基本上保持不变的,虽然总能量略微有点降低,但这是由于有限元的能量计算算法所致,不影响仿真的准确性。保险杠变形量最大的时刻是0.03s处,系统内能最大,保险杠吸能比较充分,沙漏能的变化由图看出几乎与横坐标轴相重合沙漏能很小,仿真结果有效。
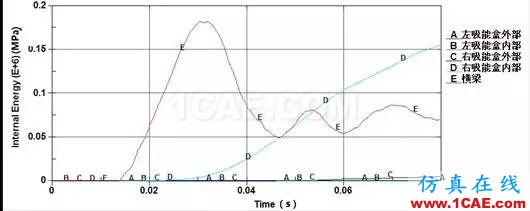
图8 各组件内能曲线
由图8可以得出左吸能盒几乎不吸收能量,碰撞产生的动能几乎都是由右吸能盒内部和横梁吸收,横梁最大吸能量为0.175*106MPa大约占总吸能量的87.5%,右吸能盒随着时间的增加吸收的能量逐渐增加。这说明该吸能盒结构需要进一步改善,从而使左右吸能盒都能够发挥作用,从而减小在碰撞过程中右吸能盒的变形。3.3 加速度分析 加速度分析结果曲线如图9所示,由结果可知,在0.03s时刻加速度达到最大,同时也证明了该仿真有效。
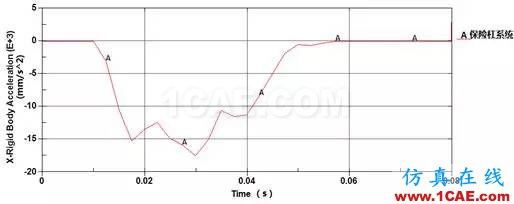
图9 加速度曲线
3.4 横梁变形分析
由于车体的撞击方向是沿X方向的,速度为4km/h,Y方向和Z方向上的速度为0,所以保险杠系统的位移变化主要在X方向上,Y方向和Z方向上位移变化很小。保险杠系统正面撞击刚性墙后,X方向上的位移最大响应如图10所示。
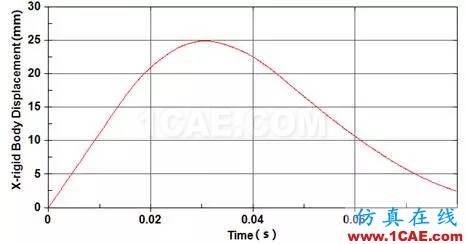
图10 横梁X方向位移
由图可以看出,横梁最大变形量在0.03s时达到峰值为25mm。按照保险杠碰撞标准,要求它在碰撞中的变形量必须小于保险杠横梁与车体间的距离。由横梁变形曲线图可知,碰撞方向的最大的结构变形量小于保险杠横梁与车体间的距离,说明该保险杠的耐撞性能较好。
本文保险杠横梁采用CFS003/LTM25碳纤维增强环氧树脂复合材料,以保险杠低速碰撞有关法规为依据,建立了保险杠低速碰撞的有限元模型,并对保险杠各组件低速碰撞动力响应特性进行仿真分析,得出以下结论:
(1)有限元法可以精确再现低速碰撞过程中,保险杠系统的变形及受力情况,从而评判其性能。
(2)低速碰撞产生的动能几乎都是由右吸能盒内部和横梁吸收,横梁最大吸能量大约占总吸能量的87.5%,说明采用碳纤维增强环氧树脂复合材料是十分有意义的。此外,右吸能盒内部随着时间的增加吸收的能量逐渐增加,而右吸能盒外部以及左吸能盒几乎不吸收能量。因此吸能盒结构需要进一步改善,从而使左右吸能盒都能够发挥作用,从而减小在碰撞过程中横梁和右吸能盒的变形。
(3)保险杠在低速碰撞条件下具有良好的耐撞性,为保险杠的设计改进提供参考依据。建议在保险杠系统设计中对保险杠和支架的刚度进行匹配以充分发挥整个保险杠系统对碰撞能量的吸收效果。
参考文献
[1] 李亦文,徐涛,徐天爽,李强,郝亮.车身低速碰撞吸能结构的优化设计[J].北京理工大学学报,2010.
[2] J.Hilmann,M.Pass,A.Haenschke,T.Vietor.Automatic concept model generation for optimization and robust design of passenger cars[J].Advances in Engineering Software.2007,(3 8):795-801.
[3] Marcus REdhe.Shape Optimization of a Vehicle Crash—box using LS-OPT[C].5th European Ls-DYNA Users’ Conference.2003:65-70.
[4] 章正伟.保险杠低速碰撞性能仿真研究[J].振动与噪声控制,2007,(4):78-81.
[5] 杨永生.汽车保险杠系统低速碰撞性能研究[D]. 哈尔滨:哈尔滨工程大学,2009:54-76.
[6] 刘玄,张晓晴.基于LS-DYNA的复合材料层合板低速冲击损伤研究[J].科学技术与工程,2012,12(12):2888-2892.
[7] 张彦.纤维增强复合材料层合结构冲击损伤预测研究[D].上海:上海交通大学,2007.
[8] 白金泽. LS-DYNA3D理论基础与实例分析[M].北京科学出版社,2005
[9] 李喆,孙凌玉.复合材料薄壁管冲击断裂分析与吸能特性优化[J].复合材料学报,2011,28(4):212-218.
作者:郭启涛,周云波,佘磊,王显会,魏然
中国汽车材料网编辑整理
相关标签搜索:【技术帖】复合材料汽车前保险杠低速碰撞仿真分析 HyperWorks有限元分析培训 HyperMesh网格划分培训 hyperMesh视频教程 HyperWorks学习教程 HyperWorks培训教程 HyperWorks资料下载 HyperMesh代做 HyperMesh基础知识 Fluent、CFX流体分析 HFSS电磁分析 Ansys培训 Abaqus培训