【模具技术】叠层式注射模具设计与应用
2017-01-08 by:CAE仿真在线 来源:互联网
叠层式注射模具设计与应用
引言
叠层式注射模具是一种高效、快捷、节能的新型注射模具,在我国已逐渐开始推广使用。与常规模具不同的是,叠层式注射模具的型腔是分布在两个或多个层面上的,呈重叠式排列,即相当于是将多副模具叠放组合在一起。
通常,注塑机与常规模具配合使用时,其本身的注射量和开模行程只使用了额定的20%~40%,没有充分发挥注塑机的性能。与常规模具相比,叠层式注射模具的锁模力只提高了5%~10%,但产量可以增加90%~95%,极大地提高了设备利用率和生产率,并降低了成本。
叠层式注射模具最适于成型大型扁平制件、浅腔壳体类制件、小型多腔薄壁制件和需大批量生产的制件。
叠层式注射模具的设计要点
叠层式注射模具作为一种新型的模具技术得到了不断的发展,特别是与热流道技术的结合,使它成为当今塑料模具发展的一项前沿技术。传统的常规模具设计理论已经不适用于叠层式注射模具设计,因此急需发展一套全新的模具设计理论以指导叠层式注射模具设计。下面将对叠层式注射模具的设计要点进行说明。
1.注塑机最大注射量
叠层式注射模具可以采用冷流道,也可以采用热流道。当使用冷流道时,需要考虑浇注系统凝料所用的塑料量;当采用热流道时,即实现无回头凝料生产,在热流道板和中心主喷嘴中的物料不影响模具所需注射量,可以忽略不计[3]。所以,在校核注塑机最大注射量时要视具体情况而定。
2.注塑机注射压力
注射压力的校核主要是检验注射压力能否满足成型的需要。对于叠层式注射模具,大多成型薄壁、投影面积大、流程长的塑件,在充填过程中需要更高的注射压力和注射速度。而叠层式热流道模具由于采用了热流道技术,相对叠层式冷流道模具来说,能较好地传递注射压力,故所需的注射压力要比叠层式冷流道模具小;但由于流程增加、投影面积增大,所需注射压力要比单层冷流道模具大。在校核注射压力时,应根据各种塑料的注塑工艺,并结合计算机模拟流动分析来确定塑件的注射压力,再与注塑机额定注射压力比较。
3.注塑机最大锁模力
叠层式注射模具的各层型腔以“背靠背”设置,理论上能在锁模力不增加的基础上在同一台注塑机上实现任意数量的叠层。但是,由于叠层式注射模具的中心主喷嘴及分流板增大了流动通道,使塑件加上浇注系统在分型面上的投影面积有所增大;并且由于叠层而延伸了流道,压力损失比常规单层模具大,注射压力相应增大,致使型腔压力增大,故锁模力有所增加,校核时按相同单层模具所需锁模力增加10%~15%是比较安全的。
4.注塑机开模行程
叠层式注射模具在两个层面分型开模并顶出塑件,当校核开模行程时,对于采用液压—机械式锁模机构的注塑机,则不需考虑模具厚度;当叠层式注射模具上具有侧向分型的抽芯机构时,则需考虑抽芯距离的影响。如果采用相同传动比的齿轮齿条或曲肘连杆开模装置等同步开模机构,则叠层式注射模具各层的行程不受制品高度的限制,其开模行程是多层模具中最大开模行程那一层的n倍(n为叠层式注射模具的层数)。
5.主喷嘴长度
中心主喷嘴不能太长或太短,这样模具闭合时,中心主喷嘴不会超出注塑机喷嘴在机座后退或前进的最大距离。由于中心主喷嘴要与模具的中间部分在分型时一起移动,所以应确保开模后中心主喷嘴仍留在定模部分内,以防止中心主喷嘴头部的溢料滴入定模型腔壁上。
6.浇注系统
叠层式注射模具既可以采用普通流道浇注系统(即冷流道浇注系统),也可以采用热流道浇注系统。热流道浇注系统能够较好地传递注射压力,有利于提高塑件的成型质量,并易于实现自动化生产,但对塑料品种有一定要求,而且热流道系统价格昂贵。当采用冷流道时,塑件的成型质量稍差,但模具加工容易,故成本较低。所以,用何种浇注系统应视具体情况而定。
7.模温控制系统
模温是影响塑件成型质量的重要因素之一,叠层式注射模具设计时应保证各层型腔的温度条件控制一致。对于叠层式热流道注射模具,为减少热流道系统由于热传导的热量损失,应减少模具与热流道板之间的接触面积,并设置相应的隔热垫块。
8.开模机构
为使塑件收缩一致,塑件在各型腔中的停留时间(冷却时间)应当相等,故叠层式注射模具应当确保各层型腔的分型面同时开启。齿轮齿条传动机构和机械式连杆机构常作为叠层式注射模具的开模机构,前者的技术性能较好,也较经济,但后者的灵活性更大。采用液压辅助开模更容易控制开模时间,但结构较大。
9.脱模机构
根据冷却时间等同要求,叠层式注射模具应对各层型腔中的塑件同时顶出,采用弹簧或者高压空气的脱模机构能够达到这一要求。
国内外叠层式注射模具的发展与应用
早在1940年12月KNOWLESER就取得了叠层式模具的专利权。今天的叠层式注射模具,不仅比传统的单层模具成本更低,而且增加了应用叠层式注射模具的灵活性。经过几十年的研究与发展,叠层式注射模具经历了冷流道双层注射模具、热流道双层注射模具、3层或4层叠层式注射模具、直角进浇热流道叠层式注射模具、旋转叠层式注射模具等结构的发展变化。
1.国外叠层式注射模具的发展动态
国外叠层式注射模具技术起步较早,发展相对成熟,知名的叠层模具公司有Tradesco、Ferromatik Milacron、Foboha和Engel等。由于热流道技术的应用在国外发展较快,所以热流道叠层式注射模具技术在国外被广泛使用。此外,发达国家在新型叠层式注射模具技术处于领先水平,最近发展起来的旋转叠层式注射模具技术拓宽了叠层式注射模具的应用能力。
20世纪60~70年代,国外一些公司便开始研制叠层式注射模具。瑞士的Schottli公司最早开发出工业应用的叠层式注射模具。
1980年德国的Johnson T.便设计了一款冷流道双层注射模具,如图1所示,该模具由动模部分、定模部分和中间部分组成,中间部分实际上就是延续了主流道并具有分流道和两层各自型腔的型腔板,在动模和定模部分都设置有脱模机构,用机械、液压或气压等方式来顶出塑件。
图1 冷流道双层注射模具
1989年D.Gener和Wiesbaden-Delkheim设计了一款热流道双层注射模具,如图2所示,它也由动模部分、定模部分和中间部分组成,中间部分由热流道和向型腔供料的热喷嘴以及制品的2个型腔板构成。1992年日本的確井裕雄和山本国雄发明了一款热喷嘴不对称分布的热流道叠层式注射模具,但合理的流道设计能够控制模腔内的熔体达到流动平衡。后来,德国的W.Homes,Bensheim,J. Li,H. Hagelstein,日本的新出毅分别设计了不同结构的热流道叠层式注射模具,其中还采用了阀浇口,在热喷嘴处多了一套阀针传动装置,控制阀针的开闭运动。
图2 热流道双层注射模具
1991年Tradesco模具公司的Rozema H.设计了一款4层叠层式注射模具,该模具是在热流道双层注射模具的基础上,延伸热流道,并增加一套中间部分使成型层数扩展到4层,使生产率提高了4倍。但并不是所有的注塑机都能达到4倍的工作量,2000年加拿大的Olaru George和Dewarm Neil发明了一种分配熔体的装置,克服了注塑机开模行程不足、注射量不够的缺点,成功地应用到4层热流道叠层式注射模具中,如图3所示。同年Tradesco模具公司成功开发了一款3层热流道叠层式注射模具,如图4所示。该设计具有在2层和4层叠层式注射模具之间中等水平的生产效率,可以使注塑生产商在塑化能力或注射压力还不足以使用4层叠层式模具的情况下,达到高于2层叠层式注射模具的生产能力。
图3 4层热流道叠层式注射模具
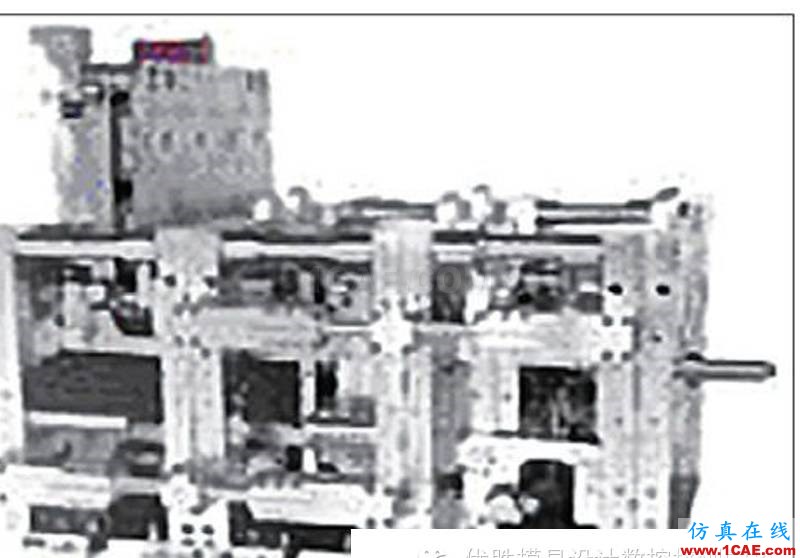
图4 3层热流道叠层式注射模具
新型叠层式模具的开发拓宽了叠层式注射模具的应用能力,使其具有多种颜色和多种材料成型的能力。旋转叠层式注射模具由在垂直轴上旋转的中心模板、动模板和定模板组成,中心模板可以有2个或4个面,当模具打开时可旋转90°或者180°。如由Engel公司开发的一种旋转模板设计,其中心模板有2个面,每个周期旋转180°。德国的Keusgen H.设计了一款旋转叠层式注射模具,如图5所示,其成型方式为在模具的一层注射一种材料进入型腔,冷却后再旋转到另一层再注射第二种材料进入型腔。而由Ferromatik Milacron欧洲公司与德国模具制造商Foboha公司合作开发的旋转叠层式注射模具有一个4个面的中心模板,每周期旋转90°。如Foboha公司申请专利的带有PET(40g)阻透层的HDPE(70g)牙膏管式瓶肩模具,其4×64的旋转叠层系统能在8.4s的周期中吐出64只双层零件,年产量达1.75×108件。丹麦的Gram技术公司设计的旋转叠层式注射模具具有多达4个边挨着边的小的中心叠层结构,各自又有4个面,并且每一周期可旋转90°
图5 旋转叠层式注射模具
2.国内叠层式注射模具的发展动态
直到20世纪80年代末,叠层式注射模具技术才逐渐传入我国模具行业,因此我国叠层式注射模具技术起步较晚,生产中采用热流道叠层式注射模具所占的比例较少,在设计和应用上与国外先进叠式模具技术存在一定的差距,甚至在一些技术领域(如旋转叠式注射模具)仍处于空白。所以,面对激烈的市场竞争,我国必须尽快提高叠层式注射模具技术,在国际市场中掌握主动性,使企业立于不败之地。
1990年北京塑料十三厂的李书赞提出了一种采用侧浇口进料的双层型腔注射模具的结构设计,如图6所示,该模具比点浇口进料减少一个模具分型面,容易实现顺序开模,但在成型较深型腔或需较大脱模力的塑件时不可靠。
图6 采用侧浇口进料的双层型腔注射模具
1992年常州轻工业学校的卜建新介绍了一种侧浇口和点浇口并用的双层型腔注射模具,如图7所示,上层型腔采用侧浇口进料,下层型腔采用点浇口进料,利用限位拉钩和限位拉板等实现顺序分型,可成型不相同的塑件。
图7 侧浇口和点浇口并用的双层型腔注射模具
1995年乙清设计一种特殊的双层注射模具,如图8所示,其流道采用了两级主流道形式,一级主流道顶部设有沉孔槽,动模板通过链条传动,带动定模部分的顶出板顶出塑件。它的缺点是需要将注塑机喷嘴延伸至模具的定模上注入主流道衬套,且浇注系统粗大。
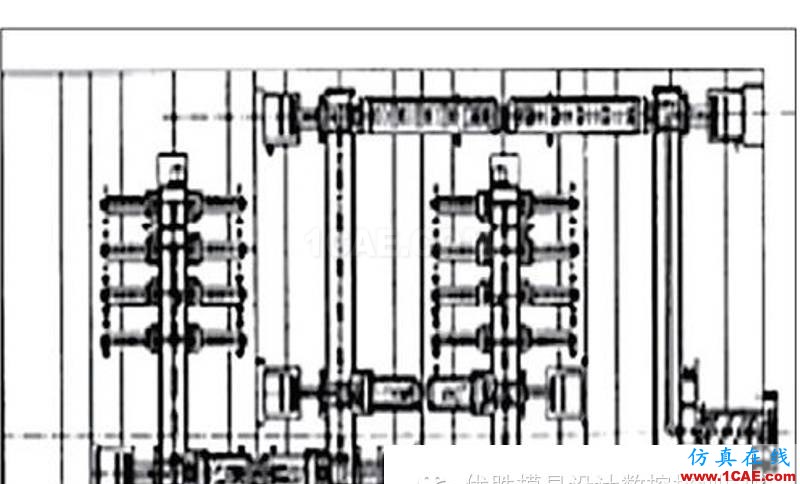
图8 采用两级主流道的双层注射模具
1997年李树、揣成智把热流道绕过中心从模具边缘将塑料熔体传送到流道板,设计了一款生产汽车门窗密封条的双层热流道注射模具,如图9所示,该模具在一个注射周期中能成型两组塑件,每组含有前后左右4条密封条,两辆汽车上使用的8条密封条即可一次成型出来。
图9 边缘传送熔体的热流道叠层式注射模具
1999年浙江伟星集团的王曰兴设计了一款高效哈夫式双层注射模具,共用一对哈夫滑块,模具结构简单,制造成本较低,而型腔数增加1倍,注塑成型周期短,生产效率高。同年王振保等人介绍了一种普通流道的双层单腔模具,如图10所示,采用正、反锥形主流道、卸料板、气压脱模和齿轮齿条分型等机构,该模具注射、脱模容易,易实现自动化生产,结构较简单,但是在第一层塑件上有流道凝料疤痕,不适于生产外观要求高的制品。后来,王振保采用主流道为热流道,其余为冷流道设计了包装盒的叠层式注射模具,该模具省去了热喷嘴,降低了成本。
图10 普通流道的双层单腔模具
2000年冯孝中等人介绍了一种潜伏式浇口的白酒杯盖双层注射模具,如图11所示,可使各层塑件与流道凝料实现模内分离,且各层分型面可同时脱出,既简化了模具结构又降低了对分型距离的要求,而且易于实现自动化生产,但要求塑件留模可靠性高和主流道衬套为深陷式。接着冯孝中又介绍了一种4层每层8个型腔的注射模具,其四级主流道依次串连,分型时自动拉断,采用摆杆同步分型、拉板脱模机构,该模具结构简单,运行可靠,比单层模具增效3倍以上,但模具流道长,充模时压降、温降大,成型工艺参数需适当调整。
图11 潜伏式浇口的白酒杯盖双层注射模具
2003年阎亚林和黄晓燕设计了一种直角进浇热流道叠层式注射模具,如图12所示,该模具改变了进浇口的位置,进浇口改在中间部分,与开模方向成直角,需要直角式注塑机,但是省去了热注道的延伸,减少了塑料熔体从注塑机喷嘴流向分流板的距离,简化了结构设计。同年陈剑玲、刘廷华等人与上海克朗宁技术设备有限公司合作,采用热流道技术,设计了浅盒形件顺序开模热流道叠层式模具,该模具含有两层型腔,提高了生产效率和设备利用率,降低了生产成本。2004年陈剑玲、刘廷华等人又设计了一款CD包装盒的热流道叠层式模具,采用定距拉杆实现顺序开模,结构紧凑,经济性佳,并节省了人力,极大地提高了效率,保证了制品质量。
图12 直角进浇热流道叠层式注射模具
2007年沈洪雷等人设计了一款光碟支架热流道叠层模具,如图13所示,该模具采用双层热流道结构形式,利用齿轮、齿条及液压缸来实现模具的顺序开模和塑件的顶出,生产的塑件尺寸和外观符合要求,生产效率大幅提高,生产成本和废品率大大下降。
图13 光碟支架热流道叠层模具
2008年王振保等人将CAE技术应用到叠层式注射模具设计中,利用Moldflow分析软件,通过对塑料填充、保压和冷却过程的模拟分析,对空调面板叠层式模具的成型过程进行动态模拟,分析了影响成型过程的主要因素,优化了工艺参数。同年贾娟娟等人以Pro/Engineer Wildfire软件为基础,通过模具专家系统EMX4.1调用和修改模架、热流道板及喷嘴,设计了一款球形摄像头内侧支架叠式热流道注射模具,并从设计过程中遇到的问题提出了对叠式模具元件的标准化要求。
结论
采用叠层式注射模具,尤其是热流道叠层式注射模具,可以充分发挥注塑机的能力,节省人力和设备资源,极大地提高生产效率。虽然叠层式注射模具在设计和加工方面成本较高,但是如果能在以下几个方面加以改进,则可以大幅度地降低模具成本,扩大其应用范围:1.完善叠层式注射模具的设计理论,缩短研发周期;2.延长一些核心元件(如加热元件、温控元件等)的使用寿命;3.使叠层式注射模具与普通的注射模塑设备配套;4.借助CAD/CAE/CAM技术进行设计、分析与加工,实现模具结构最优化;5.实现叠层式注射模具通用零件的标准化、商品化;6.提高压力传递能力,使其适于厚壁塑件的生产;7.实现叠层式注射成型工艺参数的优化;8.实现叠层式注射成型的全自动化。
随着相关技术的不断改进,叠层式注射模具在塑料制品加工工业中的应用将会不断扩大,尤其是热流道叠层式注射模具的经济性更能适应市场的需要,更能创造出巨大的经济效益,也符合我国装备制造业发展的要求,将来必有广阔的市场前景。
相关标签搜索:【模具技术】叠层式注射模具设计与应用 Moldflow分析培训 Moldflow课程培训 Moldflow注塑分析的塑胶制品应用 Moldflow视频 Moldflow技术教程 Moldflow资料下载 Moldflow分析理论 Moldflow软件下载 Fluent、CFX流体分析 HFSS电磁分析 Ansys培训 Abaqus培训