ABS和ASA部件加强筋区域出现流痕和颜色差异
2017-02-26 by:CAE仿真在线 来源:互联网
注射成型车用ABS和ASA部件,制品表面在背部有加强筋的区域出现颜色差异,导致呈现条状(甚至井字型)类似流痕的外观缺陷。The Chain里面大家从模具设计,工艺参数,热分析、流变和材料相形态等各方面进行了分析讨论,力求解决该问题。
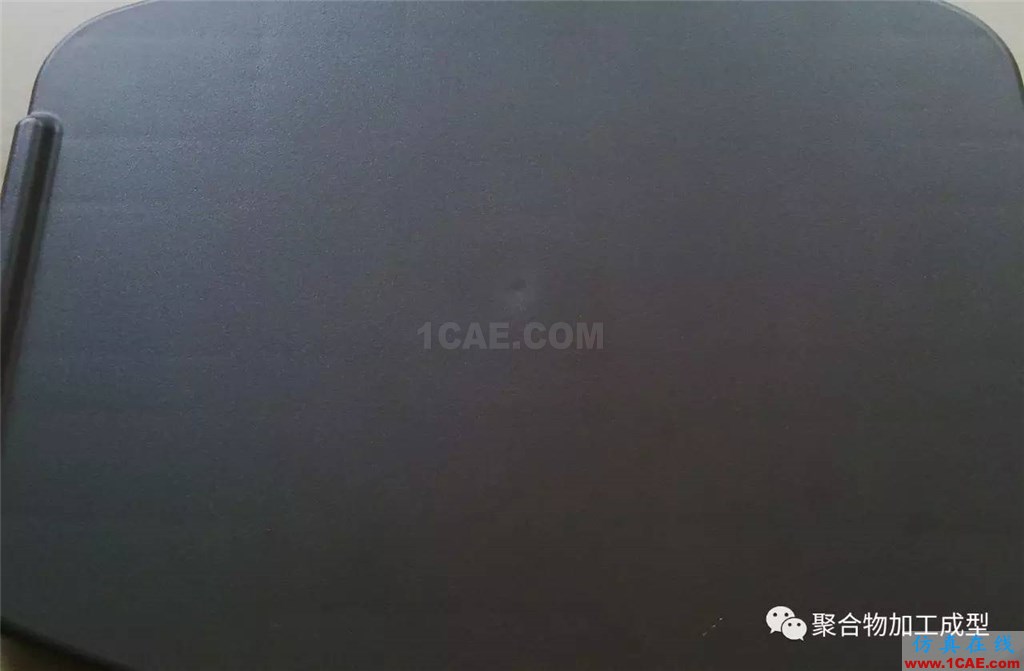
问题:
We have been facing the issue of “flow line” or “dark line” or“patches” on the injection molded components, be it light colored or darkcolored and even on the textured surface (Photo attached). This is true forboth ABS and ASA especially at the rib area. The radii at the rib sections arewell taken care. We have played with all processing parameters like temperature,inj. speed, inj. pressure etc., only to reduce the severity of appearance ofthe defect but never got it eliminated. We believe strongly that it is due torheology of the material and rubber morphology especially at the rib section.Can anybody suggest possible reason for this defect and how to overcome?.
Thanks in advance
------------------------------
Rajesh oommen
Sundaram Auto Components limited
------------------------------
讨论:
1. Nicola Pavan
Hello,
from picture are visiblea lot of sink marks, most likely in correspondence to ribs on B-side, but I'mnot sure this is the defect you mean.
Could you highlightbetter the defects on picture?
2. Amit Dharia
I see two kinds of defects. Near the rib, lines running across seem more like shrink marks and awayfrom the rib around the center light-dark patches running 90 degrees to shrinklines. Is this a center gated part? Shrink marks are due to heavy rib and willrequire different mold filling or design.
The light-dark patchesare akin to tiger stripes seen in impact modified PP, TPOs, and some TPVs. Rubber modified materials (ABS and ASA aswell as TPOs and TPEs) have a two phase morphology. Depending on the amount of rubber (Butadienein ABS), its viscosity relative to the matrix (e.g. SAN in case of ABS),injection velocity and injections pressure, two phases will flowdifferently. They also have differentfriction factor relative to the mold surface. The flow marks is due to "hesitant flow" and differentrelaxation times. If rubber particles donot have enough Mw and are not of certain size, they will also tend tocoalesce. I worked on the similar issue in TPO, we had seen replacing PP withLCBPP reduced or eliminated tiger stripes.
I suggest you try (1)Short shots to determine if this is a mold design related issue, (2) Trydifferent ABS grade of higher or lower MFR, (3) Use lubricated grade or addmold release additive to ease "stick-slip". Note that increasing melt temperature,injection pressure, and injection speeds will make this worse, (4) check moldfinish, (5) add some matting agent.
3. CRAIG SMITH
You state the rib radius are well taken care of. Did youmean that the rib thickness to wall stock thickness is good? The ribthickness should not be more than 60% of the wall thickness its connectedto. You may have to look at the gate size also if it is to small itmay be freezing off before you have sufficient enough pack. It maybe bemy screen but I don't see the tiger stripping.
4. Kevin Rottinghaus
Good morning Rajesh,
Are you speaking of thesink marks? Or is there something elsehere that I am missing.
If you are, sink marksare a packing related issue. They arecaused by the inability to adequately compensate for shrinkage. When you run into issues like this it can becaused by a variety of things such as: part geometry freezing in certain areaswhile other areas remain molten and continue to shrink, an undersized gatewhich freezes and does not allow for continued compensation, an undersizedrunner which freezes before part can be adequately packed out. The best way to investigate this would be to runa baseline comparison in mold filling simulation. This is where you model up the part, run asimulation based on your current processing parameters, and review the resultsto determine the root cause of your issue. Once this is done changes to the melt delivery system, gate, gatelocations, or part geometry (or a combination of these) can be made to reviewedto see if it improves the pack-ability.
I hope this informationhelps. Let me know if you haveadditional questions about this, or if I am mis-interpreting you problem.
Take care and i hope youhave a great week.
5. Rajesh oommen
Dear Nicola/Amit/Tim/Graig/Kevin,
Thanks a lot for your comments with good suggestions/inputs.
I would like to mention that the defect is neither “sink mark”nor “tiger stripes”. We have made surethat enough packing is given during injection molding and we use hot runnertechnology in this mold. We have carried out several Mold Flow Analysis withdifferent parameters but none of these predict the defect. Recently we increased the gate dimension alsobut with no improvement. But one of theoptions, as mentioned by Kevin, of changing the gate location could be ananswer to address the issue but at present we are not considering this as themold has already been designed.
Is this due to difference in RI at the top of the rib sectionsdue to flow difference between the rubber and SAN ??? because the whole surfaceis textured. We have already planned to change the material to a simplematerial with good flow property like PBT which could, probably, answer the reason for this defect. Alsoinline with Amit’s suggestion , we have also planned to try the presentmaterial, ASA, with a matting agent since the surface is already a textured one.
Will update in this forum on the outcome of the trials whichmay help others who are facing similar issue.
6. Tim Haake
... if you run Moldflow and are not able to predict outcomes,your inputs may be off. We offer PVT (Pressure/Volume/Temperature) instrumentsfor such a case, whereby you can actually measure your material and input the"correct' input for PVT into Moldflow. TC (Thermal Conductivity) andRheology (as we also offer) is alsohelpful in such cases and an input into Moldflow, as are many other variables.The old saying: garbage in - garbage out, comes to mind. So, either you investin testing to optimize Moldflow, or as I suggested earlier, you find anexperienced mold engineer that can help you based on his or her experience withsuch (difficult) parts.
7. Erik Foltz
Rajesh,
You stated that youdon't think the defects are sink marks. If this is true, there could be twoother reasons for the visibility of these marks. The presence of the ribsprovide more thermal mass in these areas and can cause the areas to appeardifferently. So despite not seeing or feeling the sink marks it could just bethe thermal history of the resin in these "thicker" areas. Additionally, your surface is textured, I'vefound on other applications that the way the light hits the texture/surface cancause the light to scatter differently and create a cosmetic issue, as you haveshown. Sometimes using a light analysis could highlight such an issue with thetexture.
Best of luck. Let meknow if you need anything else at this time.
8. Rajesh oommen
Hi Tim/Erik,
Thanks a lot for yourcomments. I completely agree with Tim that a proper .udb file data is very muchnecessary to run the simulation effectively, especially the PVT data. In ourcase, the .udb file has been provided by the resin manufacturer and we believeit to be true data.
I do agree with Erik that the rib impression may be due to morethermal mass at the rib area making it morphologically different from theadjacent areas. This coupled with difference in scattering of light may bereason for the dark lines at the rib area.
Thanks a lot for all your inputs and suggestions.
9. Amitkumar Dharia
Are these defects on both sides or only on one side? Do you see any surface waviness or is it flatand more of an optical effect? Are part to part weight consistent? Are vents properly located and adequate?
10. Bill Fierens
Cannot be certain of your defect, but I believe you are seeingvariation in gloss in areas not directly associated with rib structure. I have seen this in matte/textured toolingand parts (subsequently), where a temperature gradient exists. If the defects you see are in the samegeneral vicinity each shot, it could be the result of inconsistent cooling(lifters, ejector pins, etc). Localizedflow front "rupture" can occur. The root cause is difficult to resolve, as ejector pins (etc) are aninherent heat sink. Not uncommon withABS and ASA. IF your customer will allowa material alteration (within reasonable shrink limits), perhaps you might looktoward an impact-modified PMMA. Goodluck.
11. Rajesh oommen
Thanks Amit and Bill for your comments.
We would like to rephrase the defect as “rib impression” inorder to avoid confusion. The part is perfectly flat and textured. The defectis seen on only one side. The part weight is consistent. We did carry out theshort shot analysis to look at the venting system, position and is perfectlyok.
Since the part has flat surface, cooling has been well takencare. As mentioned in previous comments, we strongly believe that the ribimpression may be due to the change in morphology of the resin at the ribsurface due to the presence of rubber, butyl acrylate. A TEM analysis wouldsure throw good information on this but we need to get this done from anexternal lab. To substantiate this we used an impact modified PBT in naturalcolor and the part looks perfect!!. Sincethe modified PBT also has some rubber component (less compared to ASA), tomatch the impact property requirement, the rib impression is seen at only oneparticular angle and is not prominent but difficult to identify. The onlydisadvantage of this resin is higher density than ASA.
We are also trying out matting agent with ASA and will let youknow the results in the forum once it is done.
12. Eric Larson
Rajesh,
Interesting thread – and a challenging topic. I like your use of the term “rib impression”– it describes what you are seeing, without judgement or evaluation. It remindsme of the words a mentor of mine once used, “Don’t tell me what you think, tellme what you see.”
I do have a response to your comment: “Since the part has flatsurfaces, cooling has been well taken care of.” My response: Are you sure?
Many of the comments in this thread have mentioned thermalissues – due to a number of factors. They include thermal mass in certainareas, pressure differentials across ribs (cross flow and with the flow),temperature gradients in the mold, melt rheology of the material(s) beingmolded, texture of the mold surfaces, etc. Any of these, and all of these,could be involved.
To address this: I would recommend the use of a thermal imagingcamera. Next time you run the parts, and AFTER the process is stabilized, openthe mold and take a thermal image of the mold surfaces. I would wager thatthere will be temperature variations in the mold (that alone is a fairly safebet, as there are temperature variations in every mold), and that thosevariations are directly correlated to the “rib impressions” that you areseeing.
- Eric
P.S. How do you then fixthese issues? That is an entirely different question.
13. Rajesh oommen
Hi Eric,
Nice to read your comments. We have done the thermal image analysis also but shows no significantvariation. As you rightly mentioned the biggest question remains as to “how tofix the issue?”.
I would like to thank all the experts in this forum who havegiven their comments which are thought provoking and help to address the issuein multiple ways.
相关标签搜索:ABS和ASA部件加强筋区域出现流痕和颜色差异 Moldflow分析培训 Moldflow课程培训 Moldflow注塑分析的塑胶制品应用 Moldflow视频 Moldflow技术教程 Moldflow资料下载 Moldflow分析理论 Moldflow软件下载 Fluent、CFX流体分析 HFSS电磁分析 Ansys培训 Abaqus培训