模具技术分享 | Autoform汽车覆盖件模具全工序冲压模拟技术开发与应用
2017-04-11 by:CAE仿真在线 来源:互联网
文/唐薇 胡海 东风模具冲压技术有限公司模具分公司
模具是基础装备制造业的重要组成部分,是制造业各有关行业产业升级和技术进步的重要保障之一。随着时代的进步和科技的发展,过去长期依赖钳工、以钳工为核心的粗放型作坊式的生产管理模式,正逐渐被以技术为依托、以设计为中心的集约型现代化生产管理模式所替代。模具制造过程的前移,使调试问题被提前到加工数模设计乃至冲压工艺设计阶段解决,已经成为当前被广泛应用的模式。
目前,国际模具领先行业已广泛采用CAE 模拟仿真技术,通过前期的仿真模拟,提高模具设计质量,减少返工返修时间,提高装配、调试的效率,最终缩短调试周期,降低调试成本。其模具设计和调试过程,已经真正形成了一个闭环制造系统。
东风模具是业界处于领先地位的模具制造商,率先在国内对模具全工序冲压模拟技术做了系统的、全面的开发与应用,从技术上逐渐缩小与发达国家模具制造水平的差距,更好地满足国内汽车工业对高端覆盖件模具的需求。
一、总体思路
(1)应用虚拟冲压调试技术,在冲压工艺设计阶段实现虚拟调试,提升工艺设计水平,缩短调试周期。
(2)研究基于AUTOFORM 全工序模拟分析(SIM-MP-TB)技术,改进现有的SIM 工作流程;建立全工序冲压模拟及回弹补偿的技术标准(评价标准、经验值、标准作业书)。
(3)掌握精细化模面修正技术(A 级曲面、间隙和挠度的修正),解决轿车覆盖件的外观缺陷。建立外板表面缺陷的判断基准,建立表面缺陷的历史经验数据,积累经验,减少调试人员的工作量。
二、 主要内容及技术方案
1、全工序成形模拟技术
目前,东风模具使用的AUTOFORM是一款由瑞士开发的专业薄板成形快速模拟软件,它采用静力隐式算法进行求解,采用了全拉格朗日理论,由于对壳单元面内和横向刚度都进行了解耦,消除了刚度矩阵的病态,保证了计算的收敛性,求解速度很快。该软件可自动进行网格剖分,自动生成和交互修改压料面、工艺补充部分、拉伸筋、凹模入口线、板坯材料等网格,可以自由选择调整冲压方向,产生工艺切口,模拟重力作用、压边、成形、修边、回弹等全工序或工艺过程。
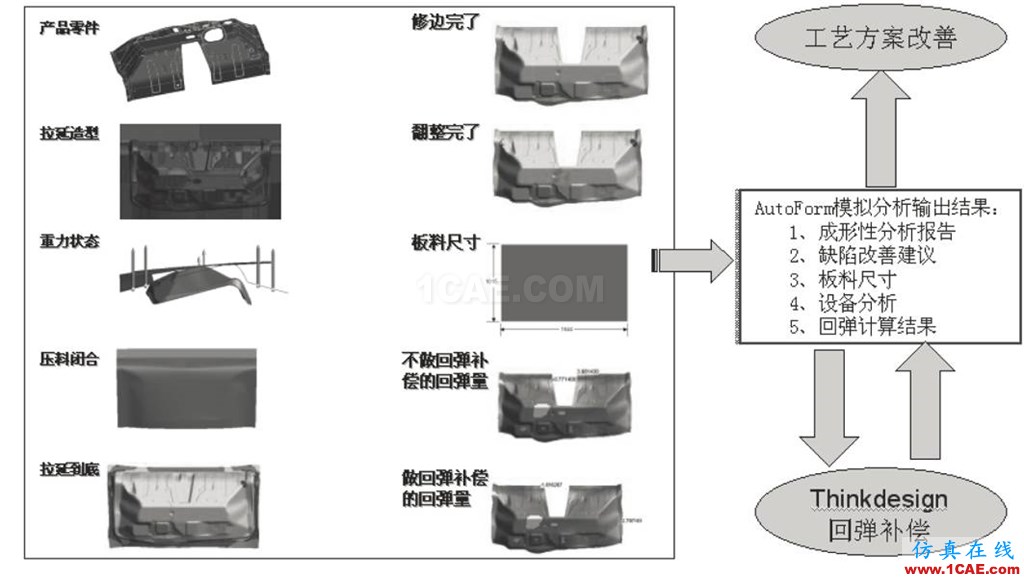
图1 Autoform 全工序成形模拟过程
在冲压工艺设计中应用AUTOFORM软件仿真模拟,一般分为三个阶段:
第一阶段是快速模面设计。在冲压工艺设计初期,用CAE软件中的快速模面设计模块设计并调整拉延工艺补充面,根据模拟结果,设计者可以很方便地对工艺补充面进行调整,直到模拟结果满足设计要求。
在前期工艺设计阶段能够改善的工艺参数有以下几点:
(1)调整冲压方向,改善缺陷处的拔模角。
(2)调整压料面的高低,以及局部的光顺性。
(3)通过改善工艺补充的型面,来控制材料的流动方向。
(4)通过改变拉延筋的阻力,来调整材料的流入量。
(5)通过改变板料的形状,以及增加刺口和切角等手段来控制材料流入。
(6)通过改变板料的材料性能,来解决缺陷问题,此方法需要得到产品设计人员的认可。
第二阶段是拉延型面的精细化仿真模拟。由于快速设计是建立在曲面的粗略构造上,曲面面片本身以及曲面面片之间的连续并非十分光顺,不能够直接用于模具表面的加工,但是对于模拟精度的影响却不是很大。因此要将第一阶段分析构造的曲面和Profile 以中性数据格式IGS 或VDA输出,在CAD 软件中进行曲面重构,得到机加工可以使用的拉延工序模具数模并进行模拟分析。此阶段的模拟分析结果直接反映出覆盖件的成形过程及产生的缺陷。工艺设计人员可以根据模拟分析过程及结果,分析缺陷产生的原因,找到解决问题的方法。
第三阶段是全工序冲压模拟。这个阶段主要是考证后序翻边整形工序是否合理,以及判定回弹的量。如果翻边时仍产生开裂与起皱,则需要重新调整工艺,同时对回弹量进行修正补偿。
2、回弹与回弹补偿技术
起皱、破裂和回弹是薄板成形中三种主要的质量缺陷,其中回弹是最难控制的,因为涉及到回弹量的准确预测,且不同材料和不同形状的冲压件的回弹规律差别很大。回弹问题的存在会影响冲压件的形状尺寸精度和表面质量,进而影响整车装配。
东风模具从2009 年开始采用Think Design GSM 模块修正冲压回弹补偿。但当时的应用处于较低的水平,采用的技术方案是:根据调试模具实物结果反馈的尺寸,人工修改回弹造型,然后修改模具。这是一种事后的、基于实物手工测量结果的措施,无法从根本上解决反复现场加工调试的问题。
与Think3 厂家多次技术交流和对需求的了解,针对东风模具的实际需求,提出相应的冲压件钣金回弹处理系统:TD Compensator,实现回弹补偿过程的自动化。此系统能够在保持原有曲面的质量上对模具型面进行修改,修改后的型面保持和原先型面相同的曲面拓补结构和曲面质量。该系统通过AUTOFORM 进行全工序模拟分析,利用Think Design 模块读取模拟分析MESH 结果,自动进行回弹补偿模面设计,获得最佳曲面质量,节省MP 设计时间40% ~ 80%,实现把回弹补偿数据加入到NC 加工数据中,在模具调试前对回弹进行预测和补偿,减少车间的反复加工、调试修改。
实施本项目的关键是:
(1)所有零件实施了全工序模拟。
(2)采购Think3 的回弹补偿模面设计模块(读取AUTOFORM MESH 数据的方式)。
(3)研究基于AUTOFORM 全工序模拟分析(SIM-MP-TB)技术,改进现有的SIM 工作流程。
(4)建立全工序冲压模拟及回弹补偿的技术标准(评价标准、经验值、标准作业书)。
(5)制定本技术的长期发展计划(从内表件到外表件,从薄板到厚板和高强度板,从MESH 数据到扫描点云数据)。
3、 外板件表面缺陷的CAE 预测
一直以来,我们认为凹陷、滑移与产品设计方案相关,很难从工艺设计、调试的角度解决,没有采取有效的技术措施,一旦发生缺陷,往往依赖现场调试减轻缺陷,而顾客默认接受缺陷。
为了解决上述问题,近年来,东风模具运用AUTOFORM 模拟分析技术,在门外板、顶盖等零件上开展了A 面修正技术的尝试( 见图2)。以零件为单位,制定零件凹陷部位图表,通过对凹陷实际数据的测量,制定“凹陷过隆”补偿标准和“强压”间隙标准;制定“过隆”补偿研磨标准作业书。用未修正的数据做模拟分析找到A面塌陷结果,确定拉延模A 面修正方案。
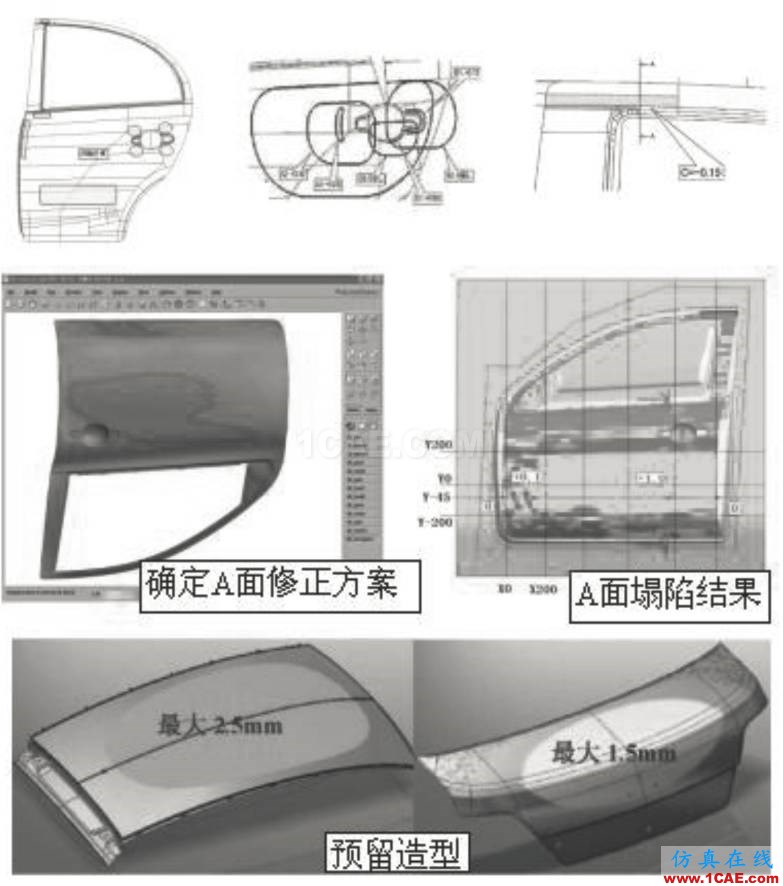
图2 修正技术的尝试
4. 建立冲压模拟分析标准
(1)为了规范AUTOFORM 软件的使用操作,避免由于软件参数设置不正确导致的运算结果不一致的情况,我们结合公司的实际情况,完成了《AUTOFORM 软件使用指令标准作业书》、《AUTOFORM软件操作说明书》及《CAE 文件的命名规范》的编写。
(2) 为了完善CAE, 建立了《CAE分析检查表》和《CAE分析典型件常见不良案例》。
(3)制定《CAE 成型品质保证单及调试跟踪记录卡》,跟踪对比CAE 模拟与车间调试的符合率情况。
(4) 制定合理的CAE 判断标准及SIM 分析风险(V1V2V3)评价标准,对起皱、变薄、板料厚度、滑移线、表面缺陷等指标作出量化规定。
(5)CAE 模拟分析材料库参数的修订和调试板料验证。
三、应用情况实例
1、D23 项目侧围零件
图3 为D23 侧围案例,由于在模拟阶段忽略了后工序的模拟,后序翻边的现场调试时由于多料而出现起皱叠料,我们通过CAE 验证分析,得到了与现场调试一样的结果。通过修改OP40 的整形形状,改善了此处的起皱问题。
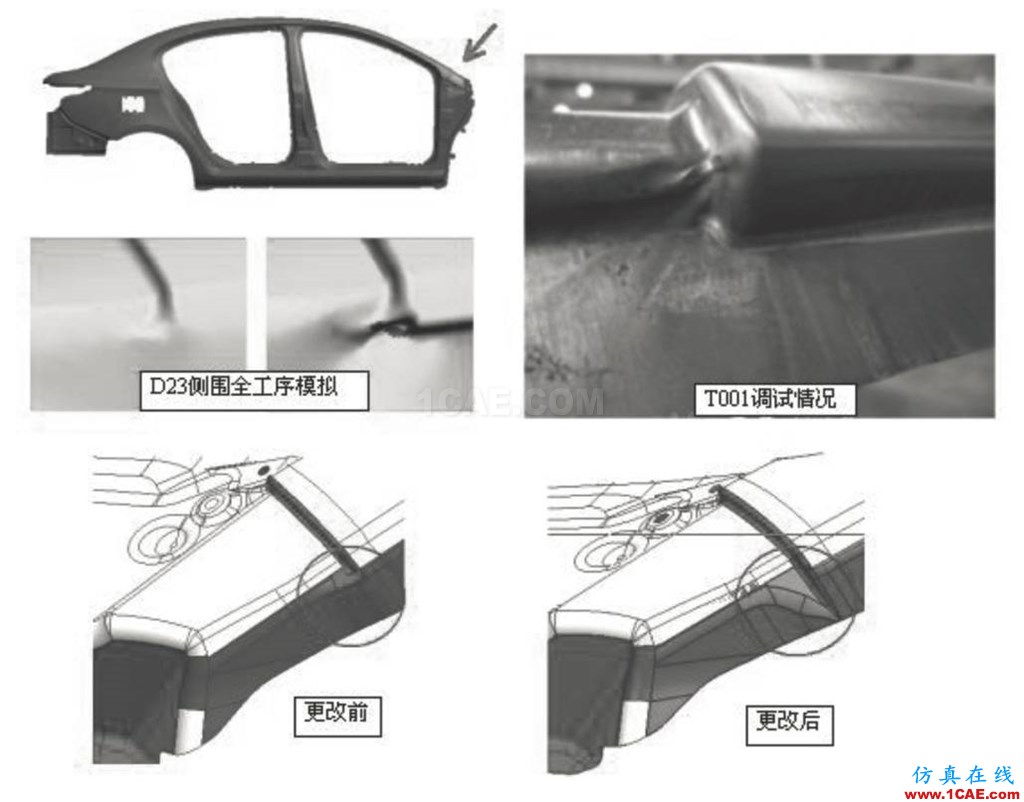
图3 CAE 分析示例1
2. Z982 项目侧围零件
图4 为Z982 侧围零件案例。
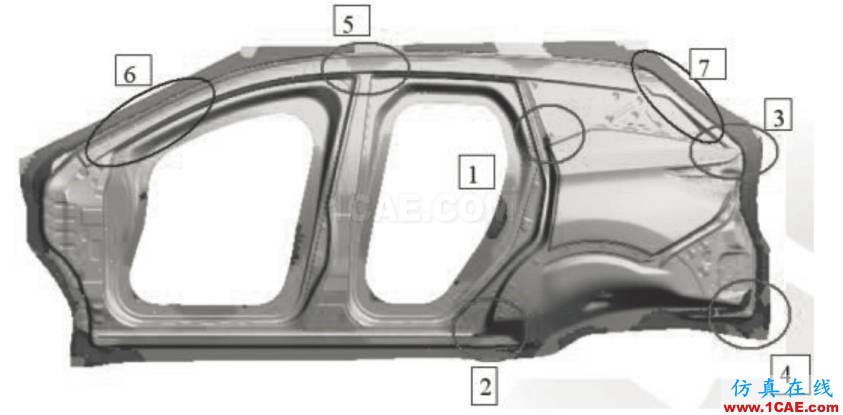
图4 CAE 分析示例2
(1)CAE 分析有开裂起皱风险,现场调试与CAE 一致,加筋,但未彻底解决问题(见图5)。
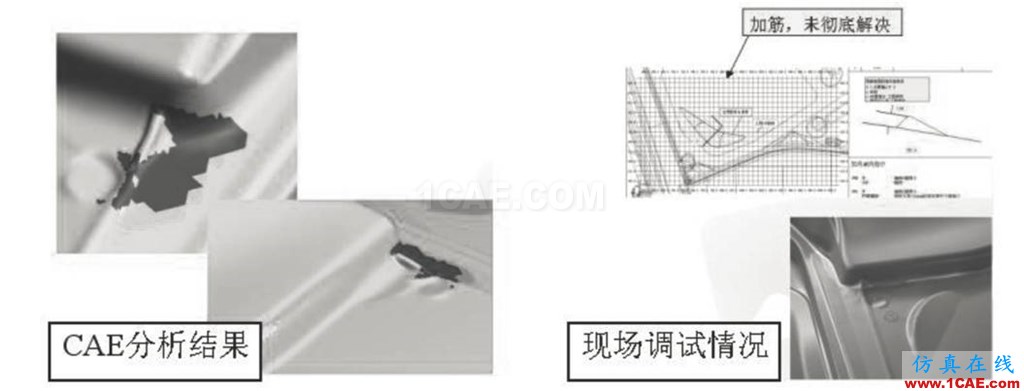
图5
(2)CAE 分析有起皱风险,现场调试与CAE 一致,改筋,增加阻力(见图6)。
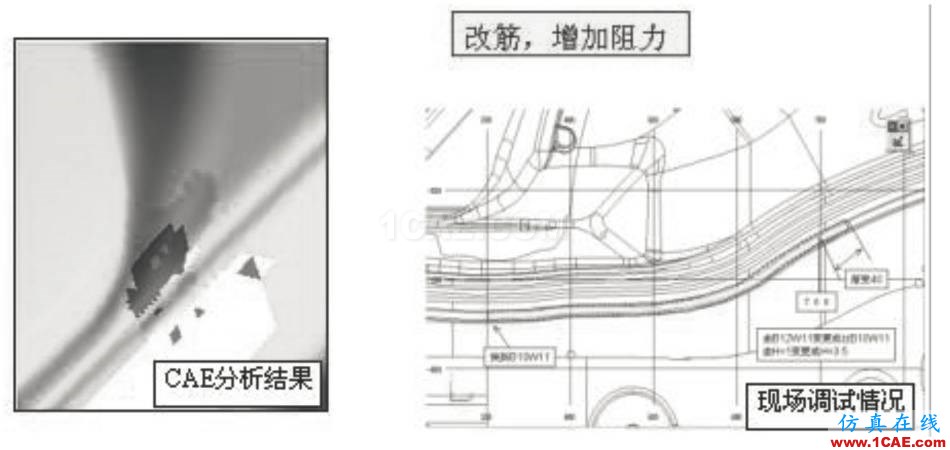
图6
(3)CAE 分析有起皱风险,现场调试与CAE 模拟一致,没有对策。
(4)下死点5mm 处时有起皱风险,调试时拉延模此处有皱,产品此处有皱( 见图7)。
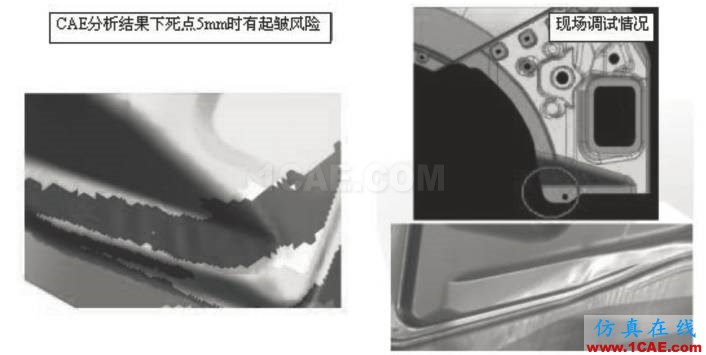
图7
(5)CAE 分析6、7 处有滑移,通过外压料圈降筋增加流入量解决( 见图8)。
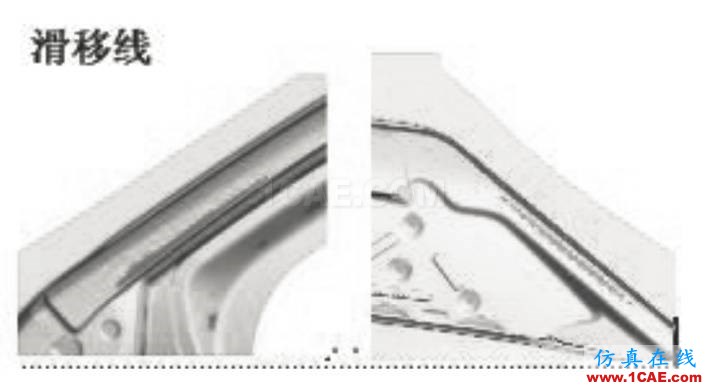
图8
3. 门外板凹陷预测及改善对策
CAE 模拟结果三处有凹陷——V1 缺陷,对策是参考CAE 分析结果,结合现场调试数据,根据零件类型制定TB 补偿方案( 见图9)。
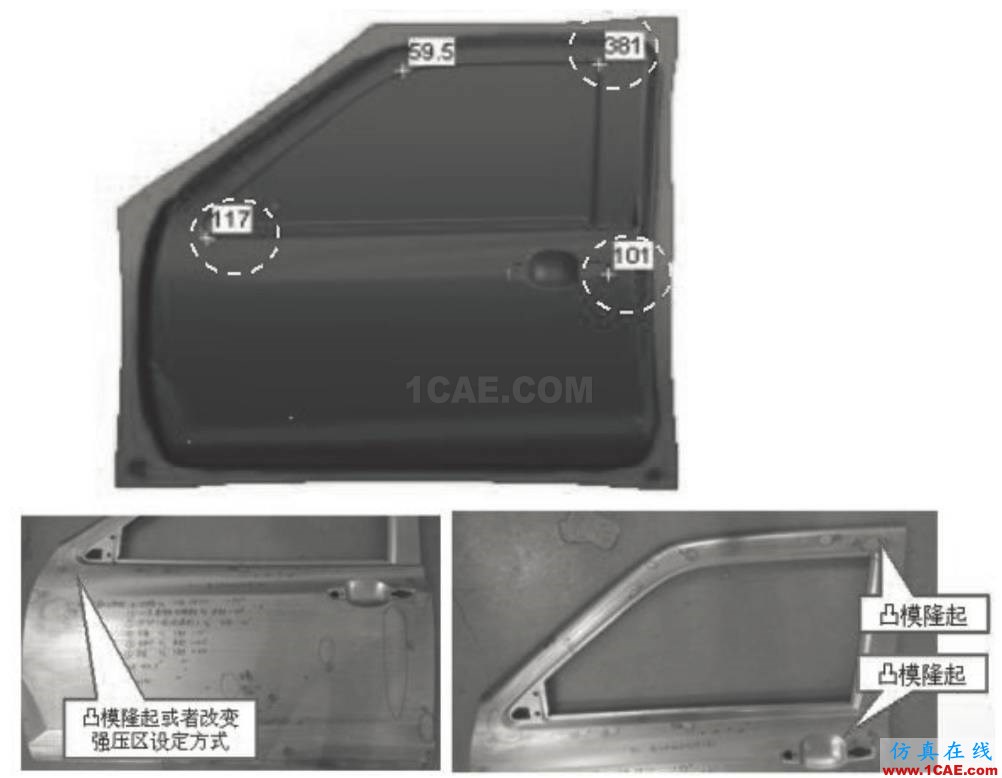
图9 凹陷预测及改善案例
4. 左/ 右前纵梁下加强板进行全工序模拟后回弹补偿
图10 是我们对左/ 右前纵梁下加强板进行全工序模拟后回弹补偿的案例:
采用AUTOFORM 分析,提供原始数模、原始网格和成型网格,导入Think Design Compensator 自动回弹补偿修改时间:32min(其中条件设定:25min,回弹计算:7min),整改回弹的过程需30min。
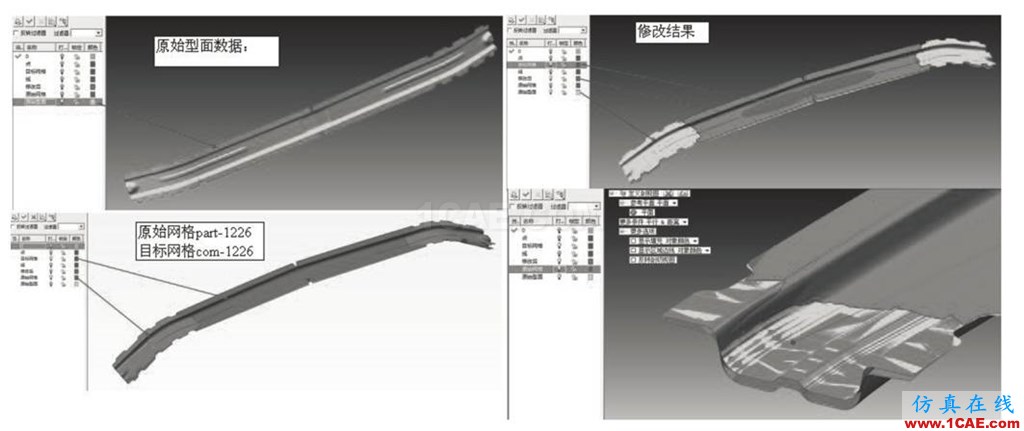
图10 左/ 右前纵梁下加强板回弹补偿案例
效益评估:
(1)曲面连续性可达到G2 连续,达到A 级曲面要求,保证了原有曲面的拓扑关系和曲面数量。
(2)之前处理类似工件需要3 ~4h,现在的设计时间可以节省65% ~ 79%,效率提高了2 ~ 4 倍。
(3)减少了反复修改的重复劳动。
四、效益分析
通过CAE 技术的应用,缩短了调试周期40% ~ 50%。更重要的是,汽车覆盖件的质量得到了大大的提高,其意义超过了缩短制造周期本身。
自动进行回弹补偿模面设计,获得最佳曲面质量,节省MP设计时间65% ~ 79%,效率提高2 ~ 4 倍。实现了把回弹补偿数据加入到NC 加工数据中,在模具调试前对回弹进行预测和补偿,减少车间的反复加工、调试和修改。不良率得到降低,保守估计在5% 以上,部分项目可减少试模1 ~ 2次,节省了直接成本。
该项目成功应用于轿车覆盖件模具的开发和制造,通过全工序模拟,提前预测和解决模具调试阶段可能出现的各类缺陷,缩短了模具制造周期,提高了零件品质,具有良好的经济效益。
五、总结与展望
东风模具率先在国内针对模具设计模拟技术进行了系统性的研究,并开发了一整套模具设计模拟的技术规范和流程,成功地应用于公司各个项目的模具设计和模具制造,使得模具设计质量得以提高,制造周期有效缩短,钳工、调试人员的劳动强度明显降低,东风模具的设计能力、制造能力和模具品质得到显著提升,产生了巨大的社会效益,在国内汽车模具行业具有极强的推广应用价值。
(内容来源:“《中国模具信息》杂志”)
相关标签搜索:模具技术分享 | Autoform汽车覆盖件模具全工序冲压模拟技术开发与应用 Autoform分析培训班 Autoform汽车模具仿真 Autoform视频教程 Autoform资料下载 在线软件培训 汽车钣金代做 Fluent、CFX流体分析 HFSS电磁分析 Ansys培训 Abaqus培训 有限元培训 Solidworks培训