导向臂支架强度及疲劳的分析与优化
2017-02-16 by:CAE仿真在线 来源:互联网
摘要:为解决某重型货车复合空气悬架导向臂支架在道路试验中失效的问题,对该导向臂支架进行了结构优化。文章利用HyperWorks软件OptiStruct模块和疲劳寿命分析软件分别对该导向臂支架进行静强度和疲劳寿命分析,根据分析结果,在HyperWorks软件的OptiStruct模块下对导向臂支架进行结构优化设计。结果表明,经过优化后的导向臂支架强度和疲劳寿命都得到提高,质量较原结构减轻13%。该方法可广泛应用于类似车辆部件的优化设计工程。
1引言
复合空气悬架系统主要由空气弹簧、导向臂、导向臂支架、高度控制阀、减震器、缓冲限位块等机械元件和电气元件,以及储气筒和空气压缩机等辅助系统组成[1]。某重型货车复合空气悬架导向臂支架在道路试验过程中发生断裂破坏的现象进行了研究,经过断口检测发现,支架破坏主要由承受极低周疲劳载荷或一次性冲击载荷引起。文章利用有限元方方法,对导向臂支架进行静强度和疲劳寿命分析并进行优化,达到提高产品性能和优化设计的目的,并为类似重型车零部件的设计与优化提供了理论计算的依据。
2导向臂支架静强度分析
2.1有限元模型
文中采用HyperMesh对某重型货车复合空气悬架导向臂支架进行网格划分,由于导向臂支架结构不规则,这里采用四面体单元,网格全局尺寸选择5mm,最终有限元模型共有节点数16256,实体单元数为62034,导向臂支架有限元模型如图1所示。
2.2约束边界条件
模型中添加刚性单元Rbe2来定义位移约束,添加刚性单元Rbe3来定义载荷作用位置。该导向臂支架模型中共添加10处用于固定约束的Rbe2,分别位于支架上端与车架连接处;1个用于载荷施加的Rbe3单元,位于支架下端导向臂连接处。
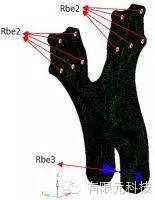
图1导向臂支架有限元模型
2.3载荷边界条件
空气悬架导向臂支架在车辆转弯、制动和加速3种极限工况下,所处工况比较恶劣,所以文章重点关注这3种工况。对整车进行动力学分析或者试验测试,可以计算或者测试出导向臂支架处的作用力和作用力矩,表1为3种工况下,作用在某重型货车空气悬架导向臂支架上的载荷,表1中的工况及载荷大小来源于整车厂对该型重卡空气悬架导向臂支架的试验测试。
表1导向臂支架工况及载荷
编号 |
载荷工况 |
FX(N) |
FY(N) |
FZ(N) |
MZ(N·m) |
1 |
转弯 |
0 |
24139 |
34484 |
15087 |
2 |
制动 |
24139 |
0 |
34484 |
0 |
3 |
加速 |
-24139 |
0 |
34484 |
0 |
2.4静强度分析
导向臂支架的材料为球墨铸铁(QT450-10),其性能参数如表2所示。
表2导向臂支架材料属性
材料 |
密度/(t/m3) |
弹性模量/GPa |
屈服强度/MPa |
泊松比 |
QT450 |
7.30 |
147 |
310 |
0.30 |
针对导向臂支架的3种载荷工况,利用HyperWorks软件的OptiStruct模块分别对其进行有限元静强度分析。经过分析可知,转弯工况下的静态位移和应力最大,空气悬架导向臂支架最大应力为345.7MPa,位于导向臂支架与车架连接孔下方节点67771位置,如图2圆圈内所示,这与道路试验破坏位置相同。导向臂支架最大位移为1.87mm,位于导向臂支架最下端节点57位置。各工况的最大变形和应力如表3所示。
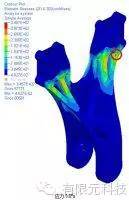
图2导向臂支架转弯工况应力云图
表3导向臂支架初始结构静强度分析结果
工况 |
最大应力(MPa) |
节点ID |
最大位移(mm) |
节点ID |
转弯 |
345.7 |
67771 |
1.870 |
57 |
制动 |
78.1 |
20148 |
0.378 |
58 |
加速 |
79.6 |
67770 |
0.378 |
47720 |
由图2和表3可知,导向臂支架在极限转弯工况时候最大应力超过材料屈服极限310MPa,所以该导向臂支架破坏形式属于极低周疲劳破坏,下面将进一步进行疲劳寿命分析。
2.5疲劳寿命分析
以OptiStruct计算得到的应力结果为输入,结合导向臂支架的材料属性、疲劳强度数据、材料统计规律、零件表面粗糙度、热处理等数据,采用FEMFAT疲劳计算软件进行计算,存活率设定为99.9%,得到导向臂支架在设定工况下的疲劳寿命安全系数云图,如图3所示。
云图中红色区域表示疲劳寿命比较低,蓝色区域表示疲劳寿命较高,由图3可见,导向臂支架最小疲劳安全系数为0.5,根据工程经验,导向臂支架的疲劳安全系数通常要求在1.32以上,所以此导向臂支架结构不能满足应用需求。疲劳寿命计算结果中最小疲劳安全系数的位置为实际试验破坏的位置,进一步确定有限元计算的可靠性,为下一步的优化分析及计算验证提供依据。
根据静强度及疲劳寿命分析,以及道路试验破坏结果可知,该导向臂支架不能满足设计需求,有必要对该零件的结构做出调整,在满足功能和装配要求的前提下,重新进行设计。
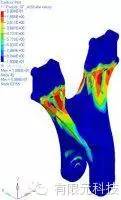
图3导向臂支架疲劳安全系数云图
3导向臂支架拓扑优化
拓扑优化是一种根据约束、载荷及优化目标而寻求结构材料最佳分配的优化方法,可采用壳单元或者实体单元来定义设计空间,并用Homogenization(均质化)和Density(密度法)来定义材料流动规律[2]。一般应用于产品结构设计的初始概念阶段,这方面目前国内外汽车业已经有了较多的研究成果。而对现有产品结构进行拓扑优化的研究相对较少[3-4],因为现有结构的造型已经形成,要在此基础上不降低结构强度,还要实现重量的下降,在产品改进设计中具有十分重要的工程意义。
在HyperMesh中把离散后的有限元模型划分成设计区域和非设计区域[5-7],定义设计变量,设计目标和约束条件,通过HyperWorks软件的OptiStruct模块对拓扑模型进行优化计算,在HyperView中进行后处理,最后利用OptiStruct模块对重新设计的优化模型做性能分析。
3.1设计空间和非设计空间
采用变密度法的连续体结构拓扑优化方法对该导向臂支架进行优化设计。单元相对密度的上下限分别为0.01和1。进行拓扑优化时,必须先确定拓扑对象的设计空间和非设计空间。设计空间为需要拓扑优化的区域,也就是设计变量,而非设计空间则是在拓扑优化过程中结构保持不变的区域。一般螺栓连接部位为非设计空间,而设计空间的确定以原结构为基础,根据零部件与周围相连部件间的静态装配关系、运动关系等条件,在保证零件之间不发生干涉的情况下尽量给出简单的设计空间。基于以上原则,而且保证在拓扑优化过程中有很大的拓扑空间,复合空气悬架导向臂支架的拓扑优化空间如图4所示。
3.2导向臂支架的拓扑优化
该导向臂支架拓扑优化主要综合考虑3种载荷工况下结构全局应力约束、某些关键点的位移约束和体积比约束等。模型全局应力约束上限值为280MPa,设定导向臂支架的体积比上限为0.5,即最多保留拓扑模型总体积的50%,另外保证优化后模型第一阶频率不低于原结构,设定载荷集中点的位移约束为最大位移1.5mm;另外,考虑设计零件的可制造性,使用脱模方向约束创建拓扑优化设计变量,允许模具沿给定方向滑动。
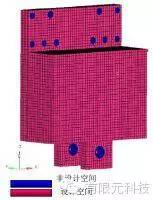
图4导向臂支架拓扑优化空间
3.3导向臂支架的优化结果
利用HyperWorks中的OptiStruct模块进行某重型货车复合空气悬架导向臂支架的拓扑优化,共经过59次优化迭代后结果收敛,图5为导向臂支架拓扑优化优化空间的材料密度分布云图。
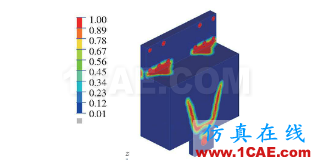
图5导向臂支架拓扑优化结果
图5中蓝色区域为可除大部分材料,材料密度值接近0,红色区域为结构需保留区域,密度值接近于1。其他颜色区域为中间区域,这些区域可去除部分材料。
把拓扑优化结果通过OptiStruct提供的OSSmooth工具进行提取,该工具可将拓扑优化结果以iges格式直接输出,输出后的几何模型如图6所示。
根据拓扑优化结果,并考虑工艺和设计经验,在三维设计软件中对原模型进行修改,得到的优化模型如图7所示,新的导向臂支架的质量为18.29kg,较原结构质量减少2.72kg,减轻质量约13%。
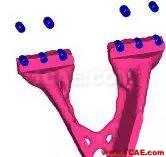

图6导向臂支架经OSSmooth提取的几何模型图7导向臂支架的优化模型
4导向臂支架优化前后性能对比
根据拓扑优化的导向臂支架结构,利用有限元软件HyperWorks的OptiStruct模块对导向臂支架进行静强度分析,利用疲劳寿命分析软件对其进行疲劳分析,并与原结构进行对比。导向臂支架优化前后各工况下最大应力对比结果见表4,转弯工况下导向臂支架应力云图如图8所示,导向臂支架在设定工况下的疲劳安全系数云图如图9所示。
表4导向臂支架优化前后各工况下性能对比
工况 |
原结构最大应力(MPa) |
新结构最大应力(MPa) |
变化量(MPa) |
百分比(%) |
转弯 |
345.7 |
255.1 |
-90.6 |
-26 |
制动 |
78.1 |
139.6 |
61.5 |
78 |
加速 |
79.6 |
133.9 |
54.3 |
67 |
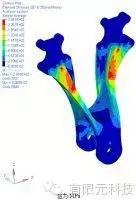
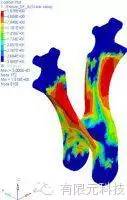
图8优化后导向臂支架转弯工况应力云图图9优化后导向臂支架疲劳安全系数云图
由表4可以看出,优化后的导向臂支架在转弯工况下最大应力为255.1MPa,比原来的结构降低了26%,强度得到极大的提高;而在加速和制动工况下,应力值有所增大,但都远低于材料的屈服极限,在可接受范围内。由图8的新结构在转弯工况下的应力云图可知,新结构的应力分布更加均匀,结构更加趋于安全;由图9可以看出,导向臂支架最小安全系数为1.519,根据工程经验,导向臂支架的疲劳安全系数满足要求。
计算结果表明,进行优化设计后的导向臂支架,给定工况下最大应力有所降低,应力分布更加均匀。通过对导向臂支架优化前后的性能比较,证明了拓扑优化设计方法在不减少结构部件强度和性能的基础上,可以有效减轻结构重量,达到了降低制造成本的目的。
优化后的结构进行了零部件试制并在安徽定远试验场进行整车耐久性试验,没有出现试验故障,证明了上述优化方案的可靠性。
5结论
以某重型货车复合空气悬架导向臂支架为分析对象,运用HyperWorks中的OptiStruct模块对其进行静强度分析,基于静强度应力结果利用疲劳寿命分析软件进行疲劳寿命预测,发现该导向臂支架静强度和疲劳寿命都不满足应用要求;利用HyperWorks平台的OptiStruct模块,将基于变密度法的连续体结构拓扑优化方法应用到该导向臂支架结构优化设计中,对多工况下的导向臂支架结构进行优化设计;根据拓扑优化的结构,再结合制造工艺及设计经验,对导向臂支架进行重新设计,最后新结构进行了应力和疲劳寿命的计算,并和优化前的数据进行比较。计算结果表明,进行优化设计后的导向臂支架,质量减轻了约13%,转弯工况应力降低26%,另外两个工况应力虽有所增加,但不影响整体性能,而且疲劳寿命安全系数达到1.519,满足工程要求,经过优化后的导向臂支架安全性能得到提升,重量减轻。
相关标签搜索:导向臂支架强度及疲劳的分析与优化 HyperWorks有限元分析培训 HyperMesh网格划分培训 hyperMesh视频教程 HyperWorks学习教程 HyperWorks培训教程 HyperWorks资料下载 HyperMesh代做 HyperMesh基础知识 Fluent、CFX流体分析 HFSS电磁分析 Ansys培训 Abaqus培训